Porous honeycomb type denitration catalyst for ship denitration, preparation method and application thereof
A technology of denitrification catalyst and porous catalyst, which is applied in the application fields of porous honeycomb denitrification catalyst for ship denitrification and its preparation, and flue gas denitrification. Resistant to pulverization and high catalytic efficiency
- Summary
- Abstract
- Description
- Claims
- Application Information
AI Technical Summary
Problems solved by technology
Method used
Image
Examples
Embodiment 1
[0031] Preparation of ammonium metavanitate solution
[0032] Add 80 liters of deionized water and 12 kg of monoethanolammonium into the ammonium metavanamate dissolving tank, heat it to 100°C by steam, then add 10 kg of ammonium metavanamate and 56 kg of ammonium metatungstate, turn on the low-speed rotary stirring, and continue The mixed liquid is heated by steam until the temperature of the ammonium metavanate dissolution tank is 98° C. and aged at this temperature for 30 minutes.
Embodiment 2
[0034] Catalyst preparation
[0035] kneading
[0036] Primary mixing: Add 390kg of anatase-type titanium dioxide into the powerful mixing machine, rotate the rotor at a low speed at 350 rpm, and run the mixing machine. Then, 2.0 kg of stearic acid, 31.5 kg of short fibers, 6.5 kg of lactic acid with a mass concentration of 50%, 230 liters of deionized water and 45 liters of ammonia water with a mass concentration of 20% were added, and the above materials were mixed and kneaded. The kneading process was to run the kneader for 15 minutes by high-speed rotation of the rotor.
[0037] Secondary mixing: After the first mixing, a certain amount of 200 kg of anatase titanium dioxide is added to the mixing machine together with 18 liters of deionized water and 8 liters of ammonia water with a mass concentration of 20%, and the second mixing is carried out. Run at high speed. When the temperature of the mixed material reaches 95°C (about 1 hour), open the exhaust valve of the knea...
Embodiment 3
[0074] Catalyst preparation
[0075] kneading
[0076] Primary mixing: Add 350kg of anatase-type titanium dioxide into the powerful kneading machine, rotate the rotor at a low speed at 350 rpm, and run the kneading machine. Then, 1.5 kg of stearic acid, 35 kg of short fibers, 4.0 kg of lactic acid with a mass concentration of 50%, 200 liters of deionized water and 50 liters of ammonia water with a mass concentration of 20% were added, and the above materials were mixed and kneaded. The kneading process was to run the kneader for 15 minutes by high-speed rotation of the rotor.
[0077] Secondary mixing: After the first mixing, a certain amount of 225 kg of anatase titanium dioxide is added to the mixing machine together with 20 liters of deionized water and 10 liters of ammonia water with a mass concentration of 20%, and the second mixing is carried out. Run at high speed. When the temperature of the mixed material reaches 95°C (about 1 hour), open the exhaust valve of the k...
PUM
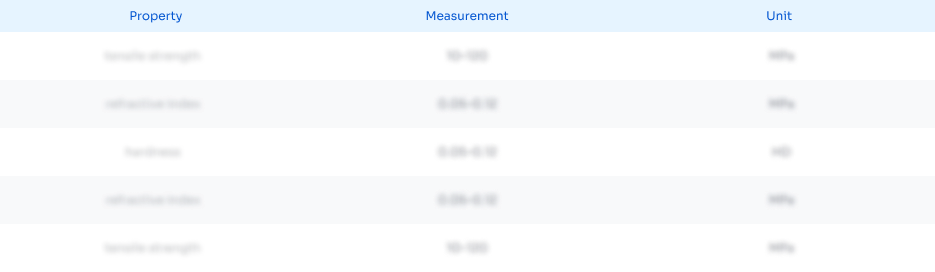
Abstract
Description
Claims
Application Information

- R&D
- Intellectual Property
- Life Sciences
- Materials
- Tech Scout
- Unparalleled Data Quality
- Higher Quality Content
- 60% Fewer Hallucinations
Browse by: Latest US Patents, China's latest patents, Technical Efficacy Thesaurus, Application Domain, Technology Topic, Popular Technical Reports.
© 2025 PatSnap. All rights reserved.Legal|Privacy policy|Modern Slavery Act Transparency Statement|Sitemap|About US| Contact US: help@patsnap.com