Efficient thermal shock joint performance test device for blade coating layer of gas turbine
A test device and thermal shock technology, applied in the direction of measurement device, strength characteristics, instruments, etc., can solve the problem of lack of thermal performance detection of the test piece, and achieve the effect of fully automating the number of experiments, improving the efficiency of the experiment, and recording the number of experiments.
- Summary
- Abstract
- Description
- Claims
- Application Information
AI Technical Summary
Problems solved by technology
Method used
Image
Examples
Embodiment Construction
[0024] Such as Figures 1 to 5 As shown, a high-efficiency thermal shock combined performance test device for a gas turbine blade coating includes a high-temperature electric furnace system, a cooling water system, an air cooling system, a test piece display device, and a control system; the test sample display device includes a The test piece basket 7 and the test piece seat 11 on the driving mechanism 12 are put into the test pieces 7 respectively, and the test piece basket 7 travels back and forth between the high-temperature electric furnace system and the cooling water system through the driving mechanism 12; The seat 11 travels back and forth between the high-temperature electric furnace system and the air-cooling system through the driving mechanism 12 . The cooling water system includes a cooling water tank 8, a drain plate 2, a filter plate 4, an air dryer 1, a circulating water pump 3, a cooling pipe 5, and a heating rod 6; the upper part of the cooling water tank 8 ...
PUM
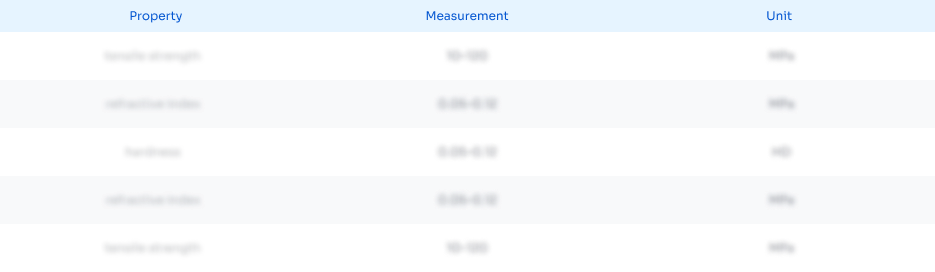
Abstract
Description
Claims
Application Information

- R&D
- Intellectual Property
- Life Sciences
- Materials
- Tech Scout
- Unparalleled Data Quality
- Higher Quality Content
- 60% Fewer Hallucinations
Browse by: Latest US Patents, China's latest patents, Technical Efficacy Thesaurus, Application Domain, Technology Topic, Popular Technical Reports.
© 2025 PatSnap. All rights reserved.Legal|Privacy policy|Modern Slavery Act Transparency Statement|Sitemap|About US| Contact US: help@patsnap.com