Locomotive cracking resistant cable material and preparation method thereof
A railway locomotive, anti-cracking technology, applied in circuits, electrical components, organic insulators, etc., can solve problems such as hindering safe evacuation and fire fighting, unable to meet market demand, loss of life and property, etc. Good insulation and performance
- Summary
- Abstract
- Description
- Claims
- Application Information
AI Technical Summary
Problems solved by technology
Method used
Examples
Embodiment Construction
[0018] An anti-cracking cable material for railway rolling stock, made of the following raw materials in weight (kg): linear low density polyethylene 85, poly-p-phenylene terephthalamide 25, basalt fiber 26, acetyl citrate three N-butyl ester 18, composite flame retardant 20, trimethylol propane cocoate 5, isostearyl laurate 4, dibutyltin dilaurate 3, monophenylene diisooctyl phosphite 2.5, distearyl Acid Hydroxy Aluminum 3, Potassium Titanate Whisker 15, Cork Powder 12, Resorcinol Monobenzoate 2.5, Nickel Dibutyl Dithiocarbamate 1;
[0019] The preparation method of described composite flame retardant is as follows:
[0020] (1) Take colemanite, montmorillonite and magnesium molybdate in a mass ratio of 4:3:1, mix them uniformly, pulverize, pass through an 80-mesh sieve, and then ball mill at 600r / min for 1h;
[0021] (2) Add water and stir the powder obtained by the above ball mill to prepare a suspension with a concentration of 40g / L, and then add a certain volume of 1mol / ...
PUM
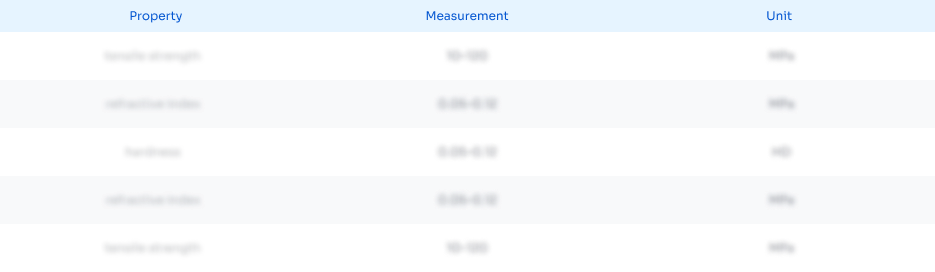
Abstract
Description
Claims
Application Information

- Generate Ideas
- Intellectual Property
- Life Sciences
- Materials
- Tech Scout
- Unparalleled Data Quality
- Higher Quality Content
- 60% Fewer Hallucinations
Browse by: Latest US Patents, China's latest patents, Technical Efficacy Thesaurus, Application Domain, Technology Topic, Popular Technical Reports.
© 2025 PatSnap. All rights reserved.Legal|Privacy policy|Modern Slavery Act Transparency Statement|Sitemap|About US| Contact US: help@patsnap.com