Low-friction modified polypropylene/glass fiber reinforced plastic composite electrical tube and manufacturing method thereof
A technology of polypropylene and power pipes, which is applied in the installation of cables and cables in underground pipelines, etc., which can solve the problems of large frictional resistance, short circuit, and stuck cables, etc., and achieve reduced friction coefficient, excellent comprehensive performance, and reduced The effect of failure probability
- Summary
- Abstract
- Description
- Claims
- Application Information
AI Technical Summary
Problems solved by technology
Method used
Image
Examples
Embodiment 1
[0026] Firstly, silicone with a weight average molecular weight of 800,000-950,000 and modified polypropylene are mixed evenly at a weight ratio of 1:1, and then put into a twin-screw extruder at 170-185°C to melt, extrude and pelletize. Then the modified masterbatch and modified polypropylene are mixed evenly according to the proportion of 2wt% silicone contained in the inner layer of the final power tube, and then the mixture and modified polypropylene are dried and passed through their respective screw rods The extruder is melted and compounded at 165-185°C, extruded, sized, drawn, cooled, and cut to obtain a two-layer composite pipe; finally, the obtained two-layer composite pipe is composited with a glass fiber reinforced layer on its outer wall according to a mechanical winding method. The cross-sectional structure shown in the drawings is a composite power tube of silicone-containing modified polypropylene low-friction layer 1, modified polypropylene layer 2 and glass fi...
Embodiment 2
[0029] First, mix the silicone with the weight average molecular weight of 1,050,000-1,200,000 and the modified polypropylene evenly in a weight ratio of 1:1, and then put it into a twin-screw extruder at 180-200°C to melt and extrude to make pellets. Then the modified masterbatch and modified polypropylene are mixed evenly according to the proportion of 3.5wt% silicone contained in the inner layer of the final power tube, and then the mixture and modified polypropylene are dried and passed through their respective The screw extruder is melted and compounded at 185-205°C, extruded, sized, drawn, cooled, and cut to obtain a two-layer composite pipe; finally, the obtained two-layer composite pipe is composited with a glass fiber reinforced layer on its outer wall according to mechanical winding. As shown in the drawings, the cross-sectional structure is a composite power tube of silicone-containing modified polypropylene low-friction layer 1, modified polypropylene layer 2 and gl...
Embodiment 3
[0032] First, mix the silicone with the weight average molecular weight of 950000-1050000 and the modified polypropylene in a weight ratio of 1:1, and then put it into a twin-screw extruder at 175-190 ° C to melt and extrude to make pellets. Then the modified masterbatch and modified polypropylene are mixed evenly according to the proportion of 2.5wt% silicone contained in the inner layer of the power tube, and then the mixture and modified polypropylene are dried and passed through their respective The screw extruder is melted and compounded at 170-190°C, extruded, sized, drawn, cooled, and cut to obtain a two-layer composite pipe; finally, the obtained two-layer composite pipe is composited with a glass fiber reinforced layer on its outer wall according to mechanical winding. As shown in the drawings, the cross-sectional structure is a composite power tube of silicone-containing modified polypropylene low-friction layer 1, modified polypropylene layer 2 and glass fiber reinfo...
PUM
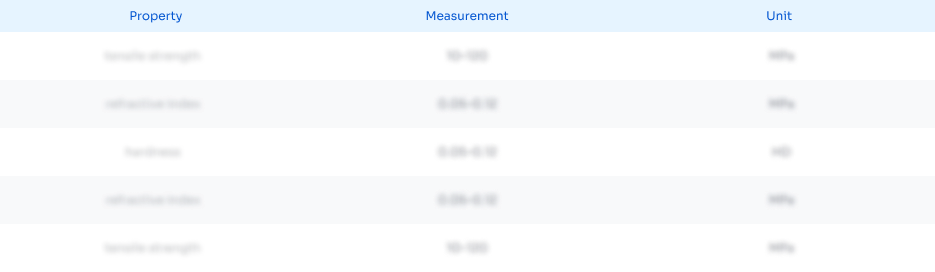
Abstract
Description
Claims
Application Information

- R&D Engineer
- R&D Manager
- IP Professional
- Industry Leading Data Capabilities
- Powerful AI technology
- Patent DNA Extraction
Browse by: Latest US Patents, China's latest patents, Technical Efficacy Thesaurus, Application Domain, Technology Topic, Popular Technical Reports.
© 2024 PatSnap. All rights reserved.Legal|Privacy policy|Modern Slavery Act Transparency Statement|Sitemap|About US| Contact US: help@patsnap.com