Environment-friendly smoke-suppression-type non-cured rubber-asphalt waterproof coating material and preparation method thereof
A kind of asphalt waterproof coating and non-curing rubber technology, which is applied in the direction of asphalt coating, coating, conjugated diene coating, etc., can solve the problems that affect the health and damage the surrounding environment, and achieve the protection of health, good waterproof performance, Emission reduction effect
- Summary
- Abstract
- Description
- Claims
- Application Information
AI Technical Summary
Problems solved by technology
Method used
Image
Examples
Embodiment 1
[0024] a. Preparation of modified asphalt: 150 kg of polyethylene wax modified asphalt and 200 kg of SBR modified asphalt were mixed to obtain modified asphalt;
[0025] B. prepare dispersant: the mixture obtained by mixing 160 kilograms of epoxy soybean oil and 120 kilograms of aromatic oil is dispersant;
[0026] c. Mix the materials in step a.b and heat up to 180°C to obtain a mixture of modified asphalt and dispersant;
[0027] d. Add 45kg of SBS to the mixture of modified asphalt and dispersant, keep the temperature at 170℃~180℃ and stir for 2 hours until completely melted;
[0028] Add 70 kg of hydrogenated rosin methyl ester, keep the temperature at 170°C and stir for 1 hour to obtain a semi-finished product;
[0029] e. Add 10 kg of expandable graphite and 200 kg of heavy calcium carbonate to the semi-finished product and stir for 2 hours to obtain a finished waterproof coating.
Embodiment 2
[0031] a. Preparation of modified asphalt: 200 kg of polyethylene wax modified asphalt and 250 kg of SBR modified asphalt were mixed to obtain modified asphalt;
[0032] B. prepare dispersant: the mixture that 200 kilograms of epoxidized soybean oil and 150 kilograms of second-line oil are mixed is dispersant;
[0033] c. Mix the materials in step a.b and heat up to 180°C to obtain a mixture of modified asphalt and dispersant;
[0034] d. Add 50kg of SBS to the mixture of modified asphalt and dispersant, keep the temperature at 170℃~180℃ and stir for 2 hours until completely melted;
[0035] Add 80 kg of hydrogenated rosin methyl ester, keep the temperature at 170° C. and stir for 1 hour to obtain a semi-finished product;
[0036] e. Add 12 kilograms of expandable graphite and 250 kilograms of heavy calcium carbonate to the semi-finished product and stir for 2 hours to obtain a finished waterproof coating.
Embodiment 3
[0038] a. Preparation of modified asphalt: 280 kg of polyethylene wax modified asphalt and 200 kg of SBR modified asphalt were mixed to obtain modified asphalt;
[0039] B. prepare dispersion agent: the mixture that 180 kilograms of epoxidized soybean oils, 156 kilograms of aromatic oils are mixed is dispersion agent;
[0040] c. Mix the materials in step a.b and heat up to 180°C to obtain a mixture of modified asphalt and dispersant;
[0041] d. Add 50.4kg of SBS to the mixture of modified asphalt and dispersant, keep the temperature at 170℃~180℃ and stir for 2 hours until completely melted;
[0042] Add 72 kg of hydrogenated rosin methyl ester, keep the temperature at 170° C. and stir for 1 hour to obtain a semi-finished product;
[0043] e. Add 9.6 kilograms of expandable graphite and 252 kilograms of heavy calcium carbonate to the semi-finished product and stir for 2 hours to obtain the finished waterproof coating.
[0044] Comparison of main indicators between ordinar...
PUM
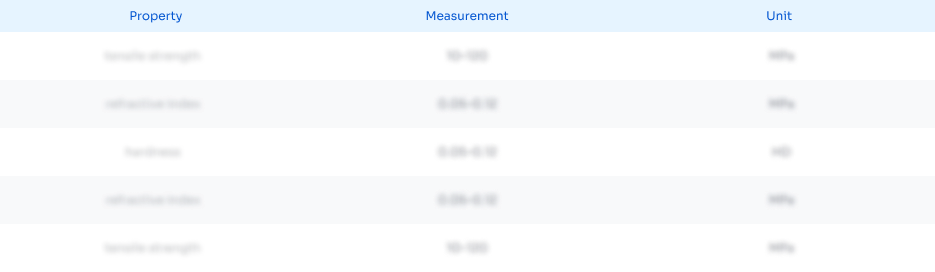
Abstract
Description
Claims
Application Information

- Generate Ideas
- Intellectual Property
- Life Sciences
- Materials
- Tech Scout
- Unparalleled Data Quality
- Higher Quality Content
- 60% Fewer Hallucinations
Browse by: Latest US Patents, China's latest patents, Technical Efficacy Thesaurus, Application Domain, Technology Topic, Popular Technical Reports.
© 2025 PatSnap. All rights reserved.Legal|Privacy policy|Modern Slavery Act Transparency Statement|Sitemap|About US| Contact US: help@patsnap.com