Stretch-forming and electromagnetic combining incremental forming method and device of large thin-wall part
A large-scale thin-walled parts, electromagnetic composite technology, applied in the direction of forming tools, metal processing equipment, manufacturing tools, etc., can solve the problems of limiting sheet metal forming accuracy, low electromagnetic forming efficiency, poor forming accuracy, etc., to improve the utilization of discharge energy Ratio, improving sheet thickness distribution, increasing the effect of forming limit
- Summary
- Abstract
- Description
- Claims
- Application Information
AI Technical Summary
Problems solved by technology
Method used
Image
Examples
Embodiment Construction
[0037] In order to make the object, technical solution and advantages of the present invention clearer, the present invention will be further described in detail below in conjunction with the accompanying drawings and embodiments. It should be understood that the specific embodiments described here are only used to explain the present invention, not to limit the present invention. In addition, the technical features involved in the various embodiments of the present invention described below can be combined with each other as long as they do not constitute a conflict with each other.
[0038] refer to Figure 2a-2e , a drawing and electromagnetic composite incremental forming device for large thin-walled parts based on a punch, including a base 1, a punch seat 2, a punch 3 arranged on the punch seat 2, a guide post 4, a guide sleeve 5, A lift cylinder 6, a drive plate 11, a plate to be deformed 12 for realizing the frame-shaped supporting plate 7 moving up and down along the ...
PUM
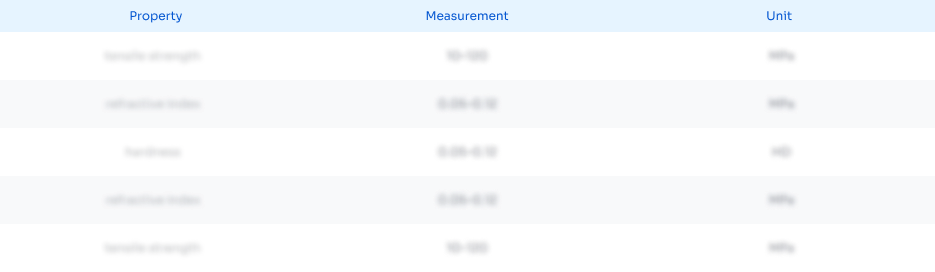
Abstract
Description
Claims
Application Information

- R&D
- Intellectual Property
- Life Sciences
- Materials
- Tech Scout
- Unparalleled Data Quality
- Higher Quality Content
- 60% Fewer Hallucinations
Browse by: Latest US Patents, China's latest patents, Technical Efficacy Thesaurus, Application Domain, Technology Topic, Popular Technical Reports.
© 2025 PatSnap. All rights reserved.Legal|Privacy policy|Modern Slavery Act Transparency Statement|Sitemap|About US| Contact US: help@patsnap.com