Engine intake pipe
A technology for intake pipes and engines, which is applied in the direction of engine components, machines/engines, mechanical equipment, etc. It can solve the problems of large differences in cylinder working conditions, uneven gas outlets, and affecting engine performance, and achieves stable dimensions and uniform gas output. , the effect of low surface roughness values
- Summary
- Abstract
- Description
- Claims
- Application Information
AI Technical Summary
Problems solved by technology
Method used
Image
Examples
Embodiment Construction
[0041] Examples such as Figure 1-4 As shown, the engine intake pipe includes a core pipe 9 made of seamless steel pipe with a rectangular cross section, the two ends of the core pipe 9 are sealed, and the outer surface of the core pipe 9 is die-cast with a shell made of aluminum material 1. The housing 1 is provided with an air inlet 3 and an air outlet 2 , the air inlet 3 communicates with the air outlet 2 , and the air inlet 3 and the air outlet 2 are set on two opposite surfaces of the housing 1 . In the air intake pipe of the present invention, the core pipe 9 made of seamless steel pipe is used inside, and the outer die-casting shell 1 ensures the smoothness of the air passage inside the air intake pipe, reduces the airflow resistance, makes the air intake more smooth, and increases the inflation efficiency . The core tube 9 is used inside and the die-casting shell 1 is used outside, which improves the density of the intake pipe, increases the strength of the intake pi...
PUM
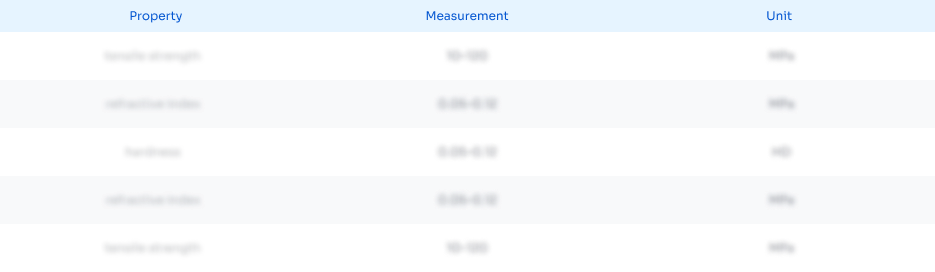
Abstract
Description
Claims
Application Information

- R&D
- Intellectual Property
- Life Sciences
- Materials
- Tech Scout
- Unparalleled Data Quality
- Higher Quality Content
- 60% Fewer Hallucinations
Browse by: Latest US Patents, China's latest patents, Technical Efficacy Thesaurus, Application Domain, Technology Topic, Popular Technical Reports.
© 2025 PatSnap. All rights reserved.Legal|Privacy policy|Modern Slavery Act Transparency Statement|Sitemap|About US| Contact US: help@patsnap.com