A kind of anorthite intermediate used as high temperature insulation material for industrial kilns
A high-temperature thermal insulation material, anorthite technology, applied in the field of anorthite thermal insulation materials and anorthite intermediates, can solve the constraints on the application and promotion of anorthite thermal insulation materials, high production costs, and factory occupation Large and other problems, to achieve the effect of improving thermal shock stability, short cycle time, and less factory occupation
- Summary
- Abstract
- Description
- Claims
- Application Information
AI Technical Summary
Problems solved by technology
Method used
Image
Examples
Embodiment 1
[0028] Get 210 g of aluminum silicate fiber and disperse it with a large amount of water to remove excess water to obtain 900 g of aluminum silicate fiber slurry, then add 1772 g of calcium silicate synthetic slurry as calcium silicate synthetic material (solid content 8.1 %, the same below, dry weight 143.5g), to obtain a mixed solution.
[0029] After stirring 210 g of calcium aluminate cement, 210 g of wollastonite, 210 g of burnt gemstone, 140 g of kyanite, and 140 g of cellulose, they were added together in the mixed solution, and finally 435 g of liquid silica sol (solid matter Content 32%, the same below, dry weight 139.2 g), stirred evenly, pressurized and dried above 100°C.
Embodiment 2
[0031] Get 420 g of aluminum silicate fiber and disperse it with a large amount of water to remove excess water to obtain 1800 g of aluminum silicate fiber slurry, then add 3444 g of calcium silicate synthetic slurry (dry weight 279.0 g) as calcium silicate synthetic material ) to obtain a mixture.
[0032] Stir 308 g of calcium aluminate cement, 252 g of coke gemstones, and 140 g of cellulose, and then add them together to the mixed solution, and finally add 435 g of silica sol (dry weight 139.2 g), stir evenly, and press to form, 100 Dry above ℃.
Embodiment 3
[0034] Take 280 g of aluminum silicate fiber, disperse it with a large amount of water and remove the excess water to obtain 1000 g of aluminum silicate fiber slurry, and then add 1772 g of calcium silicate synthetic slurry (dry weight 143.5 g) as calcium silicate synthetic material , to obtain a mixture.
[0035] 140 g of calcium aluminate cement, 210 g of wollastonite, 280 g of burnt gemstone, 210 g of aluminum hydroxide powder, and 2 g of polyacrylamide were stirred evenly, and then added to the mixed solution together, and finally 435 g of silica sol ( Dry weight 139.2 g), stir evenly, press molding, and dry above 100°C.
PUM
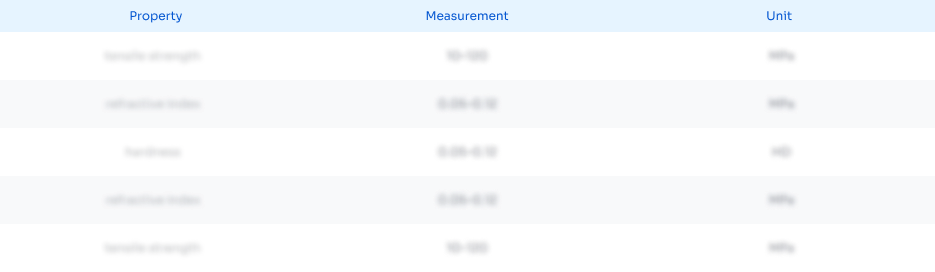
Abstract
Description
Claims
Application Information

- Generate Ideas
- Intellectual Property
- Life Sciences
- Materials
- Tech Scout
- Unparalleled Data Quality
- Higher Quality Content
- 60% Fewer Hallucinations
Browse by: Latest US Patents, China's latest patents, Technical Efficacy Thesaurus, Application Domain, Technology Topic, Popular Technical Reports.
© 2025 PatSnap. All rights reserved.Legal|Privacy policy|Modern Slavery Act Transparency Statement|Sitemap|About US| Contact US: help@patsnap.com