Preparation method of organic macromolecule polymer coating oil-water separating net
A technology of oil-water separation mesh and polymer coating, which is applied in the direction of separation methods, liquid separation, chemical instruments and methods, etc., can solve the problems of complicated process, labor-intensive, material and financial resources, and strict preparation requirements, and achieve simple operation , Low cost, stable oil-water separation ability
- Summary
- Abstract
- Description
- Claims
- Application Information
AI Technical Summary
Problems solved by technology
Method used
Image
Examples
Embodiment 1
[0046] (1) Preparation of micro-nano composite polyhedron
[0047] Prepare a mixed solution of 20.0mL divinylbenzene (DVB) and initiator 0.2g azobisisobutyronitrile (AIBN), put 1.0g of 40nm silica nanospheres prepared according to method 1 into the reactor, negative Inject the above mixed solution into the reactor under pressure and immerse the template for 1 hour, then seal the reactor and put it in a constant temperature box, pre-polymerize at 60°C for 4 hours, polymerize at 80°C for 24 hours, and peel off the homopolymer on the surface of the template after the reaction is completed , placed in hydrofluoric acid (HF) to ultrasonically disperse, remove the template, then wash with water until neutral, and vacuum dry at 60°C to obtain a solid block micro-nano composite polyhedron, and fully grind the obtained block micro-nano composite polyhedron to powder, The particle size distribution range of the powder is 100nm-5000nm (tested by Nano-ZS90 nanometer particle size and pote...
Embodiment 2
[0054] (1) Preparation of micro-nano composite polyhedron
[0055] Prepare a mixed solution of 20mL divinylbenzene (DVB) and initiator 0.2g azobisisobutyronitrile (AIBN), and put 1.0g of 300nm polyacrylamide (PAM) nanospheres prepared according to method 2 into the reactor , inject the above mixed solution into the reactor under negative pressure and immerse the template for 1 hour, then seal the reactor and put it in a constant temperature box, pre-polymerize at 60°C for 4 hours, and polymerize at 80°C for 24 hours. After the reaction is completed, the surface of the template is homopolymerized After stripping off the material, immerse in distilled water for 12 hours, remove the polyacrylamide (PAM) template, and obtain a solid block micro-nano composite polyhedron after vacuum drying at 60°C. The obtained block micro-nano composite polyhedron is fully ground to powder, and the microscopic For the micro-nano composite polyhedron, 0.22 g of it is added to 10.0 g of the ethanol...
Embodiment 3
[0060] (1) Preparation of micro-nano composite polyhedron
[0061] Prepare a mixed solution of 20mL divinylbenzene (DVB) and initiator 0.2g azobisisobutyronitrile (AIBN), and put 1.0g of 500nm polymethylmethacrylate (PMMA) nanospheres prepared according to method three into In the reactor, inject the above mixed solution into the reactor under negative pressure and immerse the template for 1 hour, then seal the reactor and put it in a constant temperature box, pre-polymerize at 60°C for 4 hours, and polymerize at 80°C for 24 hours. After the reaction is completed, the template The surface homopolymer was peeled off, soaked in ethyl acetate for 12 hours to remove the polymethyl methacrylate (PMMA) template, and after vacuum drying at 60°C, a solid block micro-nano composite polyhedron was obtained, and the obtained block micro-nano composite polyhedron was fully Grind to powder to obtain microscopic micro-nano composite polyhedron, add 0.16 g of it into 10.0 g of acetone of dis...
PUM
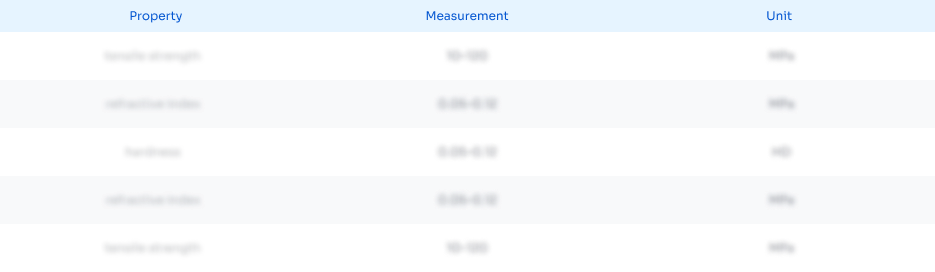
Abstract
Description
Claims
Application Information

- R&D
- Intellectual Property
- Life Sciences
- Materials
- Tech Scout
- Unparalleled Data Quality
- Higher Quality Content
- 60% Fewer Hallucinations
Browse by: Latest US Patents, China's latest patents, Technical Efficacy Thesaurus, Application Domain, Technology Topic, Popular Technical Reports.
© 2025 PatSnap. All rights reserved.Legal|Privacy policy|Modern Slavery Act Transparency Statement|Sitemap|About US| Contact US: help@patsnap.com