Preparation method and device for wafer grade white-light LED chip
An LED chip, wafer-level technology, applied in semiconductor/solid-state device manufacturing, electrical components, circuits, etc., can solve the problems of reducing packaging yield and packaging quality, high fluorescent glue content, difficult white light, etc., and achieves a simple production process. Reliable, simple and accurate operation, uniform brightness effect
- Summary
- Abstract
- Description
- Claims
- Application Information
AI Technical Summary
Problems solved by technology
Method used
Image
Examples
Embodiment 1
[0029] FIG. 1 is a specific step of preparing a wafer-level white LED chip according to the present invention. First, the epitaxially grown InGaAlN semiconductor light-emitting thin film on the silicon substrate is transferred to a conductive substrate to obtain an InGaAlN LED wafer with a vertical structure, such as Figure 1A shown. 101 in the figure is the conductive support substrate of the wafer; 102 is the dicing line gap between the chip arrays; 103 is the n-electrode pad of the chip; 104 is the blue light-emitting mesa of the InGaAlN thin film. The light emitting surface of the chip array is a nitrogen polar surface, the n electrode of the chip array is made on the nitrogen polar surface, the p electrode of the chip array is connected between the conductive substrate and the gallium nitride mesa by metal, the chip The p-electrode of the array contains metallic silver, and the light-emitting surface of the chip array is a roughened surface.
[0030] Figure 1B It is ...
Embodiment 2
[0037] Fig. 2 is another embodiment of the present invention. The difference between this embodiment and Embodiment 1 is that the mesh mask body of this solution is only an independent whole formed by interconnecting mask patterns. like Figure 2A 201 is the conductive support substrate of the wafer; 202 is the InGaAlN LED blue light chip array; 203 is the mask pattern. Wherein the pad mask pattern on the mask pattern 203 is slightly smaller than the metal pad, this is for the white light chip to not leak blue light, and the dicing line mask pattern should also be compatible with the light-emitting table of the InGaAlN LED blue light chip array 202 A certain distance is also used to obtain uniform white light on the light-emitting table, and there is no area where blue light leaks. After finishing the alignment and lamination of the mask pattern 203 and the wafer, scrape the fluorescent glue 204 on it until the fluorescent glue 204 on the mask pattern 203 is scraped clean, a...
Embodiment 3
[0040] The mesh mask body in this embodiment is also made of a mask pattern, but this mask pattern is not made on the silk screen, nor is it separated from the wafer, it is directly made on the wafer, and is separated from the wafer The wafer becomes a whole mask pattern. It can be a mask pattern formed by a certain thickness of photoresist, or a metal mask pattern electroplated on a wafer. Before coating the leveling fluorescent glue, it is necessary to level the mask pattern on the wafer. Then apply fluorescent glue on its surface, scrape off the fluorescent glue on the mask pattern, then cure the fluorescent glue, and remove the mask pattern after the fluorescent glue is cured. If it is a mask pattern formed by photoresist, remove the photoresist with a sulfuric acid hydrogen peroxide mixture, or use an organic solvent to remove the photoresist, but the photoresist and its properties cannot be damaged while removing the photoresist. If it is a mask pattern formed of metal...
PUM
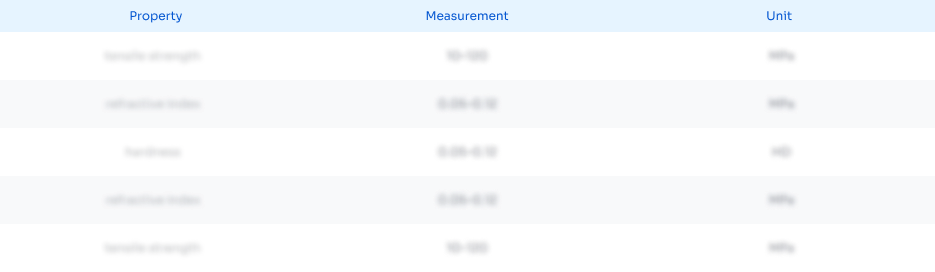
Abstract
Description
Claims
Application Information

- R&D
- Intellectual Property
- Life Sciences
- Materials
- Tech Scout
- Unparalleled Data Quality
- Higher Quality Content
- 60% Fewer Hallucinations
Browse by: Latest US Patents, China's latest patents, Technical Efficacy Thesaurus, Application Domain, Technology Topic, Popular Technical Reports.
© 2025 PatSnap. All rights reserved.Legal|Privacy policy|Modern Slavery Act Transparency Statement|Sitemap|About US| Contact US: help@patsnap.com