Full-biodegradable film and preparation method thereof
A degradable film and all-biological technology, which is applied in the composition and preparation of high-toughness fully biodegradable films, can solve the problems of poor film toughness, high price, and unacceptable cost of ordinary packaging materials, and achieve excellent toughness and full biodegradability. Guaranteed mechanical properties and low cost effects
- Summary
- Abstract
- Description
- Claims
- Application Information
AI Technical Summary
Problems solved by technology
Method used
Image
Examples
Embodiment 1
[0025] PBAT: weight average molecular weight 40kDa; molecular weight distribution: 1.9 35 parts
[0026] PLA: weight average molecular weight 110kDa; molecular weight distribution: 2.2 35 parts
[0027] PPC: weight average molecular weight 540kDa; molecular weight distribution: 3.4 29 parts
[0028] Stabilizer: 1 part stearic acid
[0029] Method: After the raw material is dried, use a twin-screw extruder with an aspect ratio of 44 to granulate. After the pellets are dried, use a single-screw extruder with an aspect ratio of 18 to blow the film. The inflation ratio is 2.8:1. 25um thick.
Embodiment 2
[0031] raw material:
[0032] PBAT: weight average molecular weight 60kDa; molecular weight distribution: 2.8 50 parts
[0033] PLA: weight average molecular weight 170kDa; molecular weight distribution: 3.3 25 parts
[0034] PPC: weight average molecular weight 660kDa; molecular weight distribution: 4.1 24 parts
[0035] Stabilizer: 1 part stearic acid
[0036] Method: After the raw material is dried, use a twin-screw extruder with an aspect ratio of 44 to granulate. After the pellets are dried, use a single-screw extruder with an aspect ratio of 18 to blow the film. The inflation ratio is 2.5:1. 20um thick.
Embodiment 3
[0038] raw material:
[0039] PBAT: weight average molecular weight 40kDa; molecular weight distribution: 1.9 60 parts
[0040] PLA: weight average molecular weight 170kDa; molecular weight distribution: 3.3 20 parts
[0041] PPC: weight average molecular weight 540kDa; molecular weight distribution: 3.4 19 parts
[0042] Stabilizer: 1 part stearic acid
[0043] Method: After the raw material is dried, use a twin-screw extruder with an aspect ratio of 44 to granulate. After the pellets are dried, use a single-screw extruder with an aspect ratio of 18 to blow the film. The inflation ratio is 3:1. 18um thick.
PUM
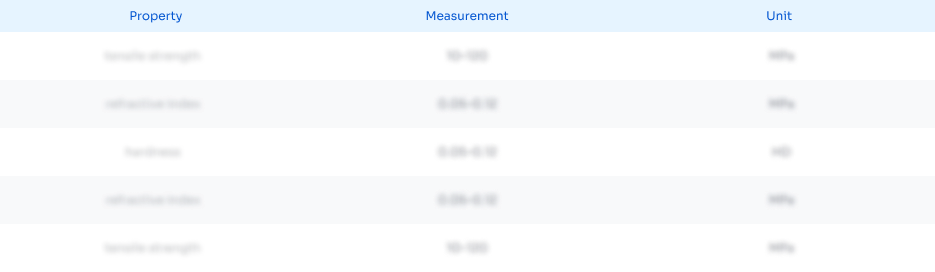
Abstract
Description
Claims
Application Information

- R&D
- Intellectual Property
- Life Sciences
- Materials
- Tech Scout
- Unparalleled Data Quality
- Higher Quality Content
- 60% Fewer Hallucinations
Browse by: Latest US Patents, China's latest patents, Technical Efficacy Thesaurus, Application Domain, Technology Topic, Popular Technical Reports.
© 2025 PatSnap. All rights reserved.Legal|Privacy policy|Modern Slavery Act Transparency Statement|Sitemap|About US| Contact US: help@patsnap.com