Polyamide acid/polyacrylonitrile-based carbon fiber and preparation method thereof
A polyacrylonitrile-based carbon fiber and polyamic acid technology, which is applied in the chemical characteristics of fibers, textiles and papermaking, etc., can solve problems such as restricting the development of carbon fibers, and achieve the effects of saving preparation costs, large output and high carbon yield
- Summary
- Abstract
- Description
- Claims
- Application Information
AI Technical Summary
Problems solved by technology
Method used
Image
Examples
Embodiment 1
[0036] A: Synthesize polyamic acid with 3,3',4,4'-biphenyltetracarboxylic dianhydride (BPDA), 4,4'-diaminodiphenyl ether (ODA), p-phenylenediamine (PDA) as raw materials (PAA) solution, and then the configured PAN solution is mixed into the PAA solution according to 30% of the mass fraction of the PAA / PAN blend solution, and the primary blended fiber is obtained by wet spinning.
[0037] B: The primary blended fiber obtained in step A is placed in a temperature-programmed oven to apply a certain draft, and the temperature is continuously raised from 200°C to 280°C to obtain PI / preoxidized PAN fiber.
[0038] C: Wrap the PI / pre-oxidized PAN fiber on a graphite plate with a certain drawing force, then place the graphite plate between two carbon films and put it into a vacuum tube furnace, and feed high-purity N2 into the vacuum tube furnace , with a heating rate of 10°C / min, the temperature was raised to 1200°C, and then kept at 1200°C for 60 minutes, and the polyamic acid / polya...
Embodiment 2
[0041] A: Synthesize polyamic acid with 3,3',4,4'-biphenyltetracarboxylic dianhydride (BPDA), 4,4'-diaminodiphenyl ether (ODA), p-phenylenediamine (PDA) as raw materials (PAA) solution, and then the configured PAN solution is mixed into the PAA solution according to 10% of the mass fraction of the PAA / PAN blend solution, and the primary blended fiber is obtained by wet spinning.
[0042] B: The primary blended fiber obtained in step A is placed in a temperature-programmed oven to apply a certain draft, and the temperature is continuously raised from 200°C to 280°C to obtain PI / preoxidized PAN fiber.
[0043] C: Wrap the PI / pre-oxidized PAN fiber on a graphite plate with a certain drawing force, then place the graphite plate between two carbon films and put it into a vacuum tube furnace, and feed high-purity N2 into the vacuum tube furnace , with a heating rate of 10°C / min, the temperature was raised to 1200°C, and then kept at 1200°C for 60 minutes, and the polyamic acid / polya...
Embodiment 3
[0045] A: Synthesize polyamic acid with 3,3',4,4'-biphenyltetracarboxylic dianhydride (BPDA), 4,4'-diaminodiphenyl ether (ODA), p-phenylenediamine (PDA) as raw materials (PAA) solution, and then the configured PAN solution is mixed into the PAA solution at 20% of the mass fraction of the PAA / PAN blend solution, and the primary blended fiber is obtained by wet spinning.
[0046] B: The primary blended fiber obtained in step A is placed in a temperature-programmed oven to apply a certain draft, and the temperature is continuously raised from 200°C to 280°C to obtain PI / preoxidized PAN fiber.
[0047] C: Wrap the PI / pre-oxidized PAN fiber on a graphite plate with a certain drawing force, then place the graphite plate between two carbon films and put it into a vacuum tube furnace, and feed high-purity N2 into the vacuum tube furnace , with a heating rate of 10°C / min, the temperature was raised to 1200°C, and then kept at 1200°C for 60 minutes, and the polyamic acid / polyacrylonitri...
PUM
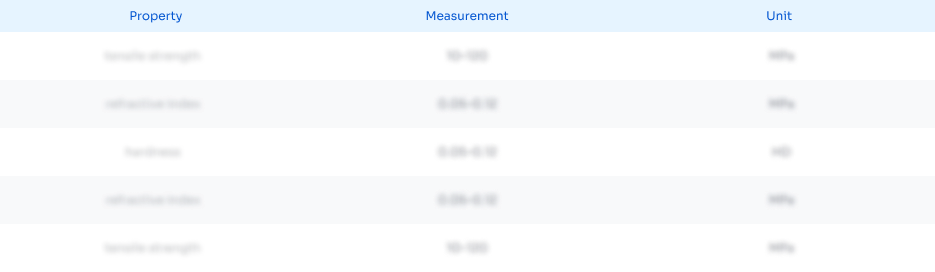
Abstract
Description
Claims
Application Information

- R&D
- Intellectual Property
- Life Sciences
- Materials
- Tech Scout
- Unparalleled Data Quality
- Higher Quality Content
- 60% Fewer Hallucinations
Browse by: Latest US Patents, China's latest patents, Technical Efficacy Thesaurus, Application Domain, Technology Topic, Popular Technical Reports.
© 2025 PatSnap. All rights reserved.Legal|Privacy policy|Modern Slavery Act Transparency Statement|Sitemap|About US| Contact US: help@patsnap.com