Fe-Ga-Al alloy strip with high magnetostrictive properties and preparation method thereof
An alloy ribbon and telescopic technology, which is applied in the direction of material selection for magnetostrictive devices, metal material coating process, device material selection, etc., can solve problems such as difficult to achieve mass production, complex process equipment, unstable process problem, to achieve the effect of being conducive to large-scale production, high degree of orientation, and strong Gaussian texture
- Summary
- Abstract
- Description
- Claims
- Application Information
AI Technical Summary
Problems solved by technology
Method used
Image
Examples
Embodiment 1
[0031] Embodiment 1: Fe of high magnetostrictive performance 83 Ga 12 al 5 Alloy strip and its preparation method
[0032] Fe, 99.99% Ga, and 99.9% Al with a purity greater than 99.9% are used, and Ga and Al are proportioned according to atomic percentages considering the burning loss of 2% and 0.5% respectively. Put the prepared raw materials into a vacuum induction furnace. After vacuuming, argon is introduced as a protective gas. After induction heating until it is completely melted, it is poured into an ingot. The alloy ingot is kept at 1100°C for 10 hours to uniform the structure composition; forged at 1150°C to form a thickness The forged alloy is hot-rolled at 1150°C; the hot-rolled alloy strip is placed in a nitriding furnace, the temperature is raised to 950°C, an ammonia atmosphere is introduced, and it is kept for 4 minutes, then taken out and air-cooled; then Warm rolling at 500°C and cold rolling at room temperature, the total reduction is 98.4%, the total numb...
Embodiment 2
[0035] Embodiment 2: Fe of high magnetostrictive performance 83 Ga 8.5 al 8.5 Alloy strip and its preparation method
[0036] Fe, 99.99% Ga and 99.9% Al with a purity greater than 99.9% are used, and the Ga and Al are proportioned by atomic percentage considering the burning loss of 2% and 0.5% respectively. Put the prepared raw materials into a vacuum induction furnace. After vacuuming, argon is introduced as a protective gas. After induction heating until it is completely melted, it is poured into an ingot. The alloy ingot is kept at 1100°C for 10 hours to uniform the structure composition; forged at 1150°C to form a thickness The forged alloy is hot-rolled at 1150°C; the hot-rolled alloy strip is placed in a nitriding furnace, heated to 900°C, introduced into an ammonia atmosphere, kept for 5 minutes, and then taken out for air cooling; then After warm rolling at 600°C and cold rolling at room temperature, the total reduction is 98.5%, the total number of passes is 23, a...
Embodiment 3
[0039] Embodiment 3: (Fe 83 Ga 8.5 al 8.5 ) 99.9 (NbC) 0.1 Alloy strip and its preparation method
[0040] Fe, 99.99% Ga, 99.9% Al, ferroniobium, and iron-carbon alloys with a purity greater than 99.9% are used. Ga and Al are proportioned according to atomic percentages considering the burning loss of 2% and 0.5% respectively. Put the prepared raw materials into a vacuum induction furnace. After vacuuming, argon is introduced as a protective gas. After induction heating until it is completely melted, it is poured into an ingot. The alloy ingot is kept at 1200 ° C for 20 hours to uniform the composition of the structure; forged at 1150 ° C to form a thickness It is a rectangular billet of 18mm; the forged alloy is hot-rolled at 1150°C; the hot-rolled alloy strip is placed in a nitriding furnace, the temperature is raised to 900°C, an ammonia atmosphere is introduced, and it is kept for 5 minutes, then taken out and air-cooled; Warm rolling at 600°C and cold rolling at room...
PUM
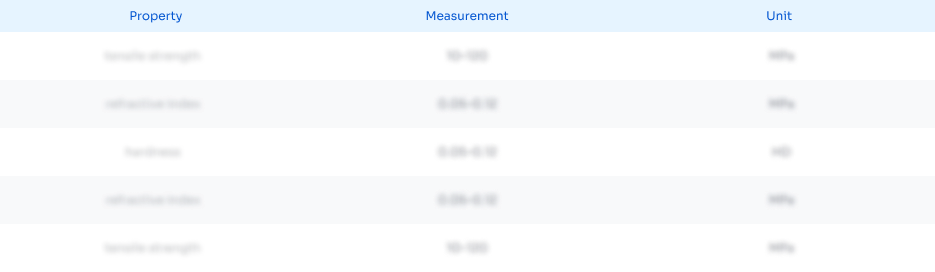
Abstract
Description
Claims
Application Information

- R&D
- Intellectual Property
- Life Sciences
- Materials
- Tech Scout
- Unparalleled Data Quality
- Higher Quality Content
- 60% Fewer Hallucinations
Browse by: Latest US Patents, China's latest patents, Technical Efficacy Thesaurus, Application Domain, Technology Topic, Popular Technical Reports.
© 2025 PatSnap. All rights reserved.Legal|Privacy policy|Modern Slavery Act Transparency Statement|Sitemap|About US| Contact US: help@patsnap.com