X-shaped guide rail of first-level transmission high-speed precise warm die forging machine
A die forging machine and guide rail technology, applied in the field of X-shaped guide rails, can solve problems such as affecting product accuracy, forging errors, clamping brakes, etc., to achieve uniform distribution of gaps, reduction of matching parts, and improved guidance.
- Summary
- Abstract
- Description
- Claims
- Application Information
AI Technical Summary
Problems solved by technology
Method used
Image
Examples
Embodiment Construction
[0034] In order to make the purpose, technical solutions and advantages of the present application clearer, the technical solutions in the embodiments will be clearly and completely described below in conjunction with the accompanying drawings in the embodiments,
[0035] See Figure 1-2 , the slider guide rail structure in the prior art is a box-type fit, the slider 2a is driven by power components such as an eccentric shaft, a connecting rod, and a motor to move on the frame 1a, and forges the workpiece A;
[0036] See Figure 3-4 , the four corners of the slider 2a have a guide plate 2a3 and two mutually perpendicular guide copper plates 2a5, a total of eight pieces, which are adjusted by the guide plate adjustment period 2a2, and the slider 2a also has a wedge-shaped guide plate 2a4.
[0037] The slider 2a with this structure is continuously heated during operation and thus expands, making the gap between the guide rails uneven and affecting the accuracy of the product; a...
PUM
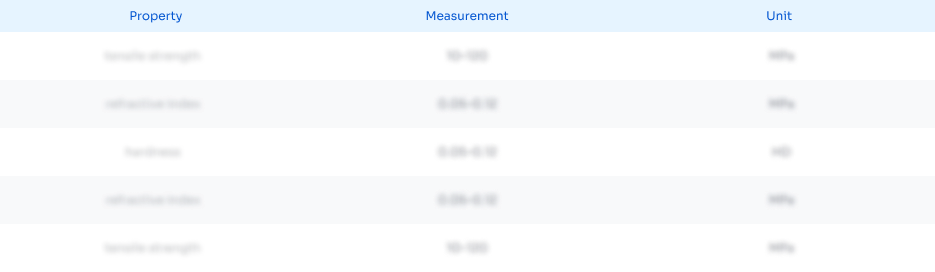
Abstract
Description
Claims
Application Information

- Generate Ideas
- Intellectual Property
- Life Sciences
- Materials
- Tech Scout
- Unparalleled Data Quality
- Higher Quality Content
- 60% Fewer Hallucinations
Browse by: Latest US Patents, China's latest patents, Technical Efficacy Thesaurus, Application Domain, Technology Topic, Popular Technical Reports.
© 2025 PatSnap. All rights reserved.Legal|Privacy policy|Modern Slavery Act Transparency Statement|Sitemap|About US| Contact US: help@patsnap.com