Method for extracting vanadium from vanadium solution through vanadium slag sodium salt roasting vanadium extraction process
A technology of sodium roasting and vanadium liquid is applied in the field of vanadium chemical industry and metallurgy, which can solve the problems of increasing the vanadium extraction rate, only 80%, polluting the environment, etc., and achieves the effect of simplifying the production process and reducing the energy consumption cost.
- Summary
- Abstract
- Description
- Claims
- Application Information
AI Technical Summary
Problems solved by technology
Method used
Image
Examples
Embodiment 1
[0024] Embodiment 1: the method technological step of vanadium extraction vanadium liquid of this vanadium slag sodiumization roasting vanadium extraction process is as follows:
[0025] (1) Calcification of vanadium precipitation: add milk of lime to the vanadium solution, the dosage (calculated as CaO) is 0.35mol, the content of (V+Si+P) in the liquid phase is 0.58mol, the temperature of vanadium precipitation is 50°C, and the reaction is 0.5 h , the calcium vanadate that obtains TV content is 22%;
[0026] (2) Acidification and transsolution: add calcium vanadate to sulfuric acid solution for transsolution, adjust the pH value of the transsolution process to 5.0, and obtain vanadium liquid and gypsum with a TV concentration of 30g / L. The reaction temperature during the transsolution process is 40°C and the reaction time is 10 min, the liquid-solid ratio of the solution process is 5:1;
[0027] (3) Purification and removal of impurities: adding aluminum sulfate to the vanad...
Embodiment 2
[0030] Embodiment 2: the method technological step of vanadium extraction vanadium liquid of this vanadium slag sodiumization roasting vanadium extraction process is as follows:
[0031] (1) Calcification of vanadium precipitation: Add quicklime to the vanadium liquid, the dosage (calculated as CaO) is 0.92 mol, the content of (V+Si+P) in the liquid phase is 0.61 mol, the temperature of vanadium precipitation is 80°C, and the reaction is 0.5 h. Obtaining TV content is the calcium vanadate of 20%;
[0032] (2) Acidification, transsolution and impurity removal: add calcium vanadate to sulfuric acid solution for transsolution, and add aluminum sulfate to the system to remove impurities, adjust the pH value of the system to 6.0, and obtain vanadium liquid and silicon-calcium slag with a TV concentration of 40g / L. The reaction temperature in the solution-removal process was 80°C, the reaction time was 20 minutes, and the liquid-solid ratio in the solution process was 10:1;
[0033...
Embodiment 3
[0035] Embodiment 3: The process steps of the method for extracting vanadium in this vanadium slag sodium roasting vanadium extracting process are as follows:
[0036] (1) Calcification of vanadium precipitation: add milk of lime to the vanadium solution, the dosage (calculated as CaO) is 1.00 mol, the content of (V+Si+P) in the liquid phase is 0.50 mol, the temperature of vanadium precipitation is 40°C, and the reaction is 0.5 h , the calcium vanadate that obtains TV content is 21%;
[0037] (2) Acidification and transsolution: add calcium vanadate to sulfuric acid solution for transsolution, adjust the pH value of the transsolution process to 7.0, and obtain vanadium liquid and gypsum with a TV concentration of 20g / L. The reaction temperature during the transsolution process is 70°C and the reaction time is 10 min, the liquid-solid ratio in the solution conversion process was 8:1;
[0038] (3) Purification and removal of impurities: adding aluminum hydroxide to the vanadium...
PUM
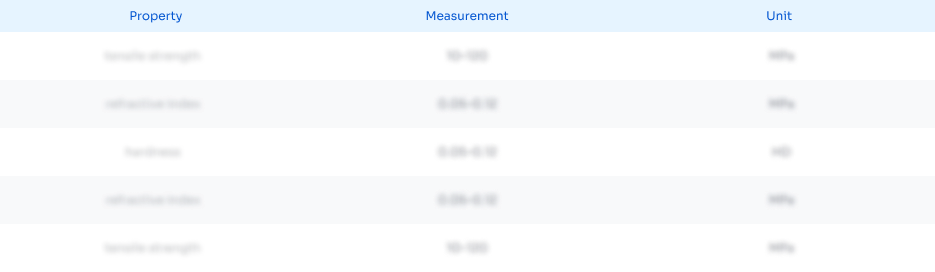
Abstract
Description
Claims
Application Information

- Generate Ideas
- Intellectual Property
- Life Sciences
- Materials
- Tech Scout
- Unparalleled Data Quality
- Higher Quality Content
- 60% Fewer Hallucinations
Browse by: Latest US Patents, China's latest patents, Technical Efficacy Thesaurus, Application Domain, Technology Topic, Popular Technical Reports.
© 2025 PatSnap. All rights reserved.Legal|Privacy policy|Modern Slavery Act Transparency Statement|Sitemap|About US| Contact US: help@patsnap.com