Carbon fiber composite material spring and manufacturing method thereof
A composite material and carbon fiber technology, applied in the direction of springs/shock absorbers, leaf springs, mechanical equipment, etc., can solve the problems of waste of materials, time-consuming, small deformation of springs, etc., and achieve the effect of less waste and low cost
- Summary
- Abstract
- Description
- Claims
- Application Information
AI Technical Summary
Problems solved by technology
Method used
Image
Examples
Embodiment 1
[0036] Embodiment 1: carbon fiber composite spring shoes
[0037]Due to the poor shock-absorbing ability of current shoes, it is not enough to prevent the damage caused by the hard ground facing the human body during continuous walking or weight-bearing activities. When walking, the weight of the entire body is transferred to a single foot, and the reaction force of the ground on the single foot reaches about 3 times the body weight. When running, the reaction force can reach 8 times the body weight. This force is transmitted upward to the bones Sometimes it is harmful to people, such as athletes, soldiers, workers, nurses, overweight people or the elderly, walking on hard roads for a long time will cause ankle shaking, knee pain, back pain, muscle fatigue, and even in some case, the tibia is fractured. In addition, current shoes cannot significantly reduce ground impact forces, which can cause muscle fatigue and reduce endurance during continuous exercise. This is because th...
Embodiment 2
[0045] Example 2: Carbon Fiber Composite Material Spring Liner Helmet
[0046] Helmets are effective in preventing skull fractures, but they are still insufficient in preventing brain injuries such as concussions. Studies show that more than 1,000,000 Americans experience concussions each year during activities as diverse as sports, driving, and construction. Traumatic brain injury can lead to severe, permanent disability or death. The deformable polymer foam currently used in helmets is too thin to prevent strong shock forces from hitting brain tissue. Concussion occurs when the soft tissue in the brain shakes when it encounters a sudden external force. Increasing the thickness of the foam will make the helmet larger and increase the weight of the helmet. It is inconvenient to wear and the comfort is also affected, so this solution is unrealistic . In addition, because the external pressure or load keeps the foam material in an irreversible state for a long time, the cush...
Embodiment 3
[0049] Example 3: Carbon Fiber Composite Material Spring Seat Cushion Chair
[0050] The carbon fiber composite material spring cushion chair can reduce the thickness and weight of the aircraft seat, which is beneficial to adding more seats and reducing the weight of the aircraft. For commercial aircraft, every pound saved can save $500 worth of fuel. However, aircraft seats must meet strict FAA (Federal Aeronautics and Space Administration) strength requirements, be able to withstand 16 times the force of gravity, and pass crash tests, which is a challenge for carbon fiber composite springs.
[0051] in reference Figure 10 Among them, the seat is equipped with carbon fiber composite material springs to form the seat structure 310, 320, 330, 340 to meet different elastic requirements. Carbon fiber composites have the disadvantage of being brittle, although they are strong they are prone to cracking under heavy impact. When designing the seat, the carbon fiber composite mat...
PUM
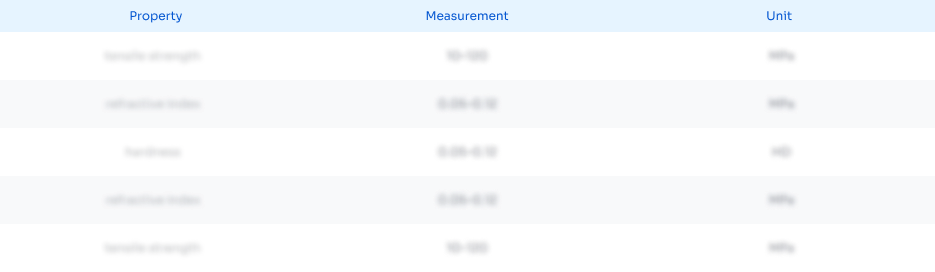
Abstract
Description
Claims
Application Information

- Generate Ideas
- Intellectual Property
- Life Sciences
- Materials
- Tech Scout
- Unparalleled Data Quality
- Higher Quality Content
- 60% Fewer Hallucinations
Browse by: Latest US Patents, China's latest patents, Technical Efficacy Thesaurus, Application Domain, Technology Topic, Popular Technical Reports.
© 2025 PatSnap. All rights reserved.Legal|Privacy policy|Modern Slavery Act Transparency Statement|Sitemap|About US| Contact US: help@patsnap.com