Composite manufacturing technique for isothermal forward and reverse combined extrusion and vacuum diffusion welding of blanket first wall
A technology of vacuum diffusion welding and composite extrusion, which is applied in the field of material processing, can solve the problems of low material utilization rate and production efficiency, inability to control forming precision, secondary free deformation of welding seam, etc., to improve material utilization rate and productivity, The effect of avoiding the decline of mechanical properties and refining the microstructure
- Summary
- Abstract
- Description
- Claims
- Application Information
AI Technical Summary
Problems solved by technology
Method used
Image
Examples
Embodiment Construction
[0027] In this embodiment, the cladding first wall isothermal positive and negative composite extrusion and vacuum diffusion welding composite manufacturing process is:
[0028] The vertical process splitting scheme is adopted, and the rectangular flow channel of the first wall of the cladding is split up and down to form an H-shaped section, and only a U-shaped section is formed in the upper and lower sealing parts to ensure the stability of the forming process.
[0029] The isothermal precision plastic forming process is used to manufacture the H-section U-shaped part and the U-shaped cross-section U-shaped part 4 of the first wall of the cladding, so as to ensure that the flow channel has equal cross-section, equal wall thickness, flat end surface, complete distribution of streamlines along the contour, and microstructure. Refinement; Specifically, the isothermal front and back composite extrusion process is used to manufacture the H-shaped cross-section U-shaped part 3 flow...
PUM
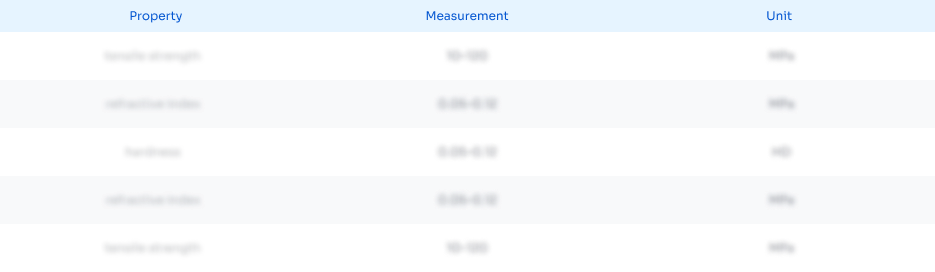
Abstract
Description
Claims
Application Information

- Generate Ideas
- Intellectual Property
- Life Sciences
- Materials
- Tech Scout
- Unparalleled Data Quality
- Higher Quality Content
- 60% Fewer Hallucinations
Browse by: Latest US Patents, China's latest patents, Technical Efficacy Thesaurus, Application Domain, Technology Topic, Popular Technical Reports.
© 2025 PatSnap. All rights reserved.Legal|Privacy policy|Modern Slavery Act Transparency Statement|Sitemap|About US| Contact US: help@patsnap.com