Kettle type hydrogenation method for paraffin or microcrystalline wax
A technology of microcrystalline wax and paraffin wax, which is applied in the refining of petroleum wax, can solve the problems of poor reactivity, long hydrogenation time, and low efficiency, and achieve the effect of less investment and simple process
- Summary
- Abstract
- Description
- Claims
- Application Information
AI Technical Summary
Problems solved by technology
Method used
Examples
Embodiment 1
[0019] In a one-liter hydrogenation kettle, open the lid of the kettle, add 20 grams of pre-sulfurized catalyst, then add 500 grams of yellow-brown No. 80 microcrystalline wax, cover, tighten the screws, check the seal, and feed nitrogen to the 12 MPa. One hour, the pressure drop is less than 1% as qualified. Let go of the nitrogen, and then replace it with nitrogen at 10MPa. Release the nitrogen to normal pressure, and vacuum to -0.09MPa. Start hydrogenation, the temperature reaches 150°C, and the pressure of the kettle is 9.0MPa. Add hydrogen, continue heating, the pressure of the kettle rises, the temperature rises to 280°C, and the pressure of the kettle reaches 12.0MPa, and desulfurization and denitrogenation are carried out for 5 hours. Then the temperature was lowered to 220°C, and the pressure in the kettle was lowered to 11.0MPa, and the hydrogenation and saturation operation of polycyclic aromatic hydrocarbons was carried out. The hydrogenation was carried out for...
Embodiment 2
[0022] In a 300-liter hydrogenation reactor, put 200kg of microcrystalline wax from the feeding pipe, add 10kg of unsulfurized columnar catalyst from the hand hole, add 0.3kg of dimethyl disulfide, seal the hand hole cover and feed Pipe valve, test pressure with 12.0MPa nitrogen, the pressure drop is less than 1% in one hour. Exhaust nitrogen, vacuumize to -0.09MPa, introduce hydrogen to 2.0MPa, and then keep at 150°C for 1 hour, and at 230°C, 290°C, and 320°C for 2 hours each to perform pre-vulcanization. null.
[0023] The desulfurization and denitrogenation operations are the same as those in Example 1. Desulfurization and denitrogenation were carried out at 280°C and 12.0 MPa for 5 hours, and hydrogenation was continued at 240°C for 3 hours.
[0024] After the above main operations are completed, lower the temperature, reduce the pressure, and cool down. The pressure of the kettle is 6.0 MPa at room temperature, and the finished product is extracted with a vacuum.
[002...
Embodiment 3
[0027] In the hydrogenation reactor of 300 liters, there is the hydrogenation catalyst 10kg (seeing embodiment 2) of sulfuration activation in interior. Drop into No. 10 mixed crystal wax (between paraffin wax and microcrystalline wax) 210kg that has been branded from feeding pipe. When the temperature reaches 120°C, all the connecting valves of the reaction kettle are closed, vacuumed to -0.09MPa, filled with nitrogen to normal pressure, and then vacuumed to -0.095MPa. Start to feed hydrogen, and the pressure in the kettle rose to 9.0MPa. Stop the hydrogen flow, start to heat up, and start stirring, the temperature rises to 300°C, and the pressure reaches 13.0MPa at this time, and the pressure drops slowly as the hydrogenation reaction proceeds. At this point, hydrogen was added to keep the pressure of the hydrogenation tank at 13.0 MPa, and the reaction was maintained for 4 hours. Lower the reaction temperature to 250°C and react for 2 hours. Cool down after the reaction,...
PUM
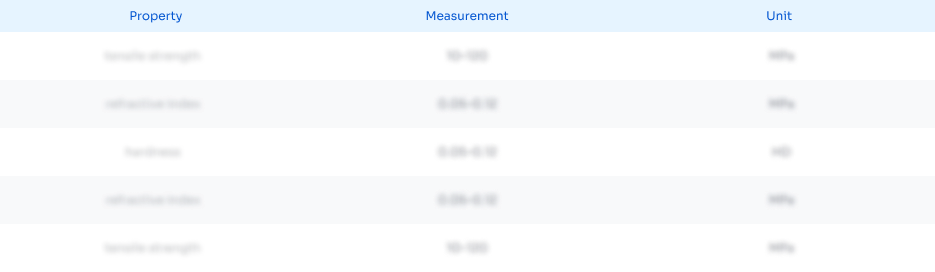
Abstract
Description
Claims
Application Information

- Generate Ideas
- Intellectual Property
- Life Sciences
- Materials
- Tech Scout
- Unparalleled Data Quality
- Higher Quality Content
- 60% Fewer Hallucinations
Browse by: Latest US Patents, China's latest patents, Technical Efficacy Thesaurus, Application Domain, Technology Topic, Popular Technical Reports.
© 2025 PatSnap. All rights reserved.Legal|Privacy policy|Modern Slavery Act Transparency Statement|Sitemap|About US| Contact US: help@patsnap.com