Modified composite cable sheath material and preparation method thereof
A sheath material and composite cable technology, applied in the direction of insulating cables, cables, circuits, etc., can solve the problems that the excellent properties cannot be fully utilized, the mechanical and mechanical properties of polymers are reduced, and the outer layer of the cable is aging and dry, so as to weaken the rubber Aging process, improvement of physical and mechanical properties, good effect of physical and mechanical properties
- Summary
- Abstract
- Description
- Claims
- Application Information
AI Technical Summary
Problems solved by technology
Method used
Examples
Embodiment 1
[0016] A modified composite cable sheath material proposed by the present invention, its raw materials include by weight: 30 parts of chlorosulfonated polyethylene, 30 parts of cross-linked insulating polyethylene, 15 parts of modified nano-kaolin, dibenzothiazole disulfide 1.3 parts, 1 part of zinc oxide, 2 parts of zinc dimethyl dithiocarbamate, 0.8 parts of anti-aging agent 4010NA, 50 parts of high wear-resistant carbon black, 20 parts of calcined clay, 25 parts of nano calcium carbonate, diphthalic acid 0.5 parts of octyl ester, 2 parts of stearic acid, 1 part of chlorinated paraffin, 3 parts of solid calcium zinc stabilizer, and 1 part of phosphite.
[0017] In the preparation process of modified nano-kaolin, 40 parts of nano-kaolin will be taken in parts by weight, and sodium hydroxide solution is added thereto so that the pH value of the material obtained is 8, and the weight-to-volume ratio of sodium hydroxide solution and nano-kaolin (g : ml) at 1:20, stir evenly, ult...
Embodiment 2
[0019] A modified composite cable sheath material proposed by the present invention, its raw materials include by weight: 40 parts of chlorosulfonated polyethylene, 20 parts of cross-linked insulating polyethylene, 20 parts of modified nano-kaolin, dibenzothiazole disulfide 0.8 parts, 3 parts of zinc oxide, 1 part of zinc dimethyl dithiocarbamate, 1.5 parts of anti-aging agent 4010NA, 40 parts of high wear-resistant carbon black, 30 parts of calcined clay, 15 parts of nano calcium carbonate, diphthalic acid 2 parts of octyl ester, 1 part of stearic acid, 2 parts of chlorinated paraffin, 1 part of solid calcium zinc stabilizer, 3 parts of phosphite.
[0020]In the preparation process of modified nano-kaolin, 20 parts of nano-kaolin will be taken by weight, and sodium hydroxide solution is added thereto so that the pH value of the material obtained is 10, and the weight-to-volume ratio of sodium hydroxide solution and nano-kaolin (g : ml) is 1:15, stir evenly, ultrasonically dis...
Embodiment 3
[0022] A modified composite cable sheath material proposed by the present invention, its raw materials include by weight: 36 parts of chlorosulfonated polyethylene, 26 parts of cross-linked insulating polyethylene, 17.4 parts of modified nano-kaolin, and 1.15 parts of dibenzothiazole disulfide 1.6 parts of zinc oxide, 1.5 parts of zinc dimethyl dithiocarbamate, 1.2 parts of antioxidant 4010NA, 45.4 parts of high wear-resistant carbon black, 26 parts of calcined clay, 21 parts of nano calcium carbonate, dioctyl phthalate 1.2 parts of ester, 1.5 parts of stearic acid, 1.6 parts of chlorinated paraffin, 2.3 parts of solid calcium zinc stabilizer, and 1.4 parts of phosphite.
[0023] In the preparation process of modified nano-kaolin, 32 parts of nano-kaolin will be taken in parts by weight, and sodium hydroxide solution is added thereto so that the pH value of the material obtained is 9, and the weight-to-volume ratio of sodium hydroxide solution and nano-kaolin (g : ml) was 1:18...
PUM
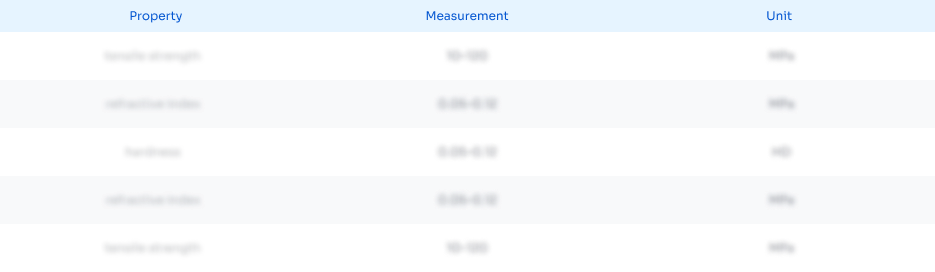
Abstract
Description
Claims
Application Information

- R&D Engineer
- R&D Manager
- IP Professional
- Industry Leading Data Capabilities
- Powerful AI technology
- Patent DNA Extraction
Browse by: Latest US Patents, China's latest patents, Technical Efficacy Thesaurus, Application Domain, Technology Topic, Popular Technical Reports.
© 2024 PatSnap. All rights reserved.Legal|Privacy policy|Modern Slavery Act Transparency Statement|Sitemap|About US| Contact US: help@patsnap.com