Flame retardant waterborne polyurethane and preparation method thereof
A technology of water-based polyurethane and polyether diol, which is applied in the field of flame-retardant water-based polyurethane, can solve the problems of poor flame-retardant effect and non-environmental protection, and achieve the effects of improving flame-retardant effect, slowing down the burning rate, and inhibiting the progress of combustion reaction
- Summary
- Abstract
- Description
- Claims
- Application Information
AI Technical Summary
Problems solved by technology
Method used
Image
Examples
Embodiment 1
[0024] (1) Dehydrate the polyether glycol and 2,2-dimethylolpropionic acid in a vacuum at 120°C and 4kPa for 2.0 hours respectively, and then seal and store for later use;
[0025] (2) Add 30 parts of toluene diisocyanate into a closed reactor with high-speed disperser, thermometer and high-purity nitrogen protection, and mix 4 parts of 2,2-dimethylolpropionic acid and 55 parts of polyether diisocyanate. The alcohol mixture was heated to 120°C to dissolve the 2,2-dimethylolpropionic acid, cooled to room temperature, and then added to the above reactor, and then 1 part of dibutyltin dilaurate was added in a nitrogen atmosphere, Stir and react for 4.0h at 700r / min at 70°C to obtain polyurethane prepolymer;
[0026] (3) Dissolve 4.0 parts of triethylamine and 0.5 parts of 3-aminopropylethoxysilane in 8 parts of deionized water at 5°C, and slowly add the above-mentioned prepolymer at a shear rate of 100rpm and 30m / s rotor speed high-speed shear emulsification for 30 minutes, add 0.5 ...
Embodiment 2
[0029] (1) Dehydrate the polyether glycol and 2,2-dimethylolpropionic acid in a vacuum at 125°C and 4.5kPa for 3.0 hours respectively, and then seal them for later use;
[0030] (2) Add 40 parts of toluene diisocyanate in a closed reactor with high-speed disperser, thermometer and high-purity nitrogen protection, and mix 10 parts of 2,2-dimethylolpropionic acid and 65 parts of polyether diisocyanate. The alcohol mixture was heated to 130°C to dissolve the 2,2-dimethylolpropionic acid, cooled to room temperature and then added to the above reactor, and then 3 parts of dibutyltin dilaurate were added in a nitrogen atmosphere, Stir and react for 4.5h at a speed of 1000r / min at 75°C to obtain a polyurethane prepolymer;
[0031] (3) Dissolve 9 parts of triethylamine and 2.0 parts of 3-aminopropylethoxysilane in 14 parts of deionized water at 10°C, slowly add the above-mentioned prepolymer, at a shear rate of 180rpm, 50m / s rotor speed high-speed shear emulsification for 40 minutes, add...
Embodiment 3
[0034] (1) Dehydrate the polyether glycol and 2,2-dimethylolpropionic acid in a vacuum at 122°C and 4.5kPa for 2.5 hours, and then seal them for later use;
[0035] (2) Add 35 parts of toluene diisocyanate in a closed reactor with high-speed disperser, thermometer and high-purity nitrogen protection, and mix 6 parts of 2,2-dimethylolpropionic acid and 60 parts of polyether diisocyanate. The alcohol mixture was heated to 125°C to dissolve the 2,2-dimethylolpropionic acid, cooled to room temperature and then added to the above reactor, and then 2 parts of dibutyltin dilaurate were added in a nitrogen atmosphere, Stir and react for 4.5h at a speed of 800r / min at 70°C to obtain a polyurethane prepolymer;
[0036] (3) Dissolve 6 parts of triethylamine and 1.3 parts of 3-aminopropylethoxysilane in 10 parts of deionized water at 6°C, and slowly add the above-mentioned prepolymer at a shear rate of 150rpm and 40m / The rotor speed of s is high-speed shear emulsification for 35 minutes, 1.4...
PUM
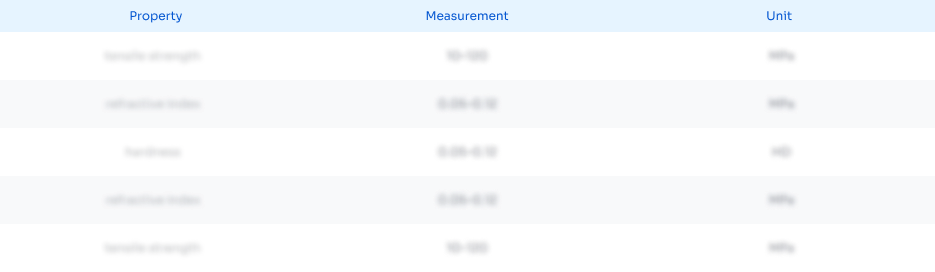
Abstract
Description
Claims
Application Information

- R&D Engineer
- R&D Manager
- IP Professional
- Industry Leading Data Capabilities
- Powerful AI technology
- Patent DNA Extraction
Browse by: Latest US Patents, China's latest patents, Technical Efficacy Thesaurus, Application Domain, Technology Topic, Popular Technical Reports.
© 2024 PatSnap. All rights reserved.Legal|Privacy policy|Modern Slavery Act Transparency Statement|Sitemap|About US| Contact US: help@patsnap.com