Hybrid Janus nano-particles obtained through polymer grafting modification as well as preparation method and application thereof
A nanoparticle and polymer technology, which is applied in the field of rubber and plastic fillers, can solve the problems of difficult dispersion and a large number of aggregation during processing.
- Summary
- Abstract
- Description
- Claims
- Application Information
AI Technical Summary
Problems solved by technology
Method used
Image
Examples
Embodiment 1
[0031] Add 100mL cyclohexane, 50mL isoprene, 0.4mL 2.7mol / L n-butyllithium to a 250mL sealed and strictly dried round-bottomed flask. The magnetron rotates at 500rpm and reacts at 25℃ for 1h. Vacuum the residue. Monomers and solvents. Disperse 0.2g of dried Janus nanoparticles into 100mL of cyclohexane, add 1mL of tetrahydrofuran, and directly add to the above polymerization system, adjust the speed to 700rpm, keep the temperature at 35℃, add 3mL of methanol after 15h, centrifuge and then ultrasonically disperse In toluene, soak in a high-speed centrifuge for 3 hours to separate, repeat more than 10 times to ensure that there is no residual free polymer, and centrifuge to obtain figure 1 The filler described.
Embodiment 2
[0033] Add 100mL cyclohexane, 35mL butadiene, 0.4mL 2.7mol / L n-butyllithium to a 250mL sealed and strictly dry round bottom flask. The magnetron rotates at 500rpm and reacts at 25℃ for 1h. Use a vacuum pump to clean the remaining monomer. Body and solvent. Disperse 0.2g of dried Janus nanoparticles into 100mL of cyclohexane, add 1mL of tetrahydrofuran, and directly add to the above polymerization system, adjust the speed to 700rpm, keep the temperature at 35℃, add 3mL of methanol after 15h, centrifuge and then ultrasonically disperse In toluene, soak in a high-speed centrifuge for 3 hours to separate, repeat more than 10 times to ensure that there is no residual free polymer, and centrifuge to obtain figure 1 The filler described.
Embodiment 3
[0035] Add 100mL cyclohexane, 50mL butadiene, 9mL distilled styrene, 0.5mL 2.7mol / L 4-cyclohexane isobutyl lithium into a 250mL sealed and strictly dry round bottom flask, the magnetron rotation speed is 500rpm, 25 React at ℃ for 1 hour, use a vacuum pump to remove residual monomers and solvents, disperse 0.2g of dried Janus nanoparticles into 100mL of cyclohexane, add 1mL of tetrahydrofuran, and directly add to the above polymerization system, adjust the speed to 700rpm, and keep the temperature Add 3mL methanol after 15h at 35℃, centrifuge and then ultrasonically disperse in toluene, soak in a high-speed centrifuge for 3h, repeat more than 10 times to ensure that there is no residual free polymer. figure 1 The filler described.
PUM
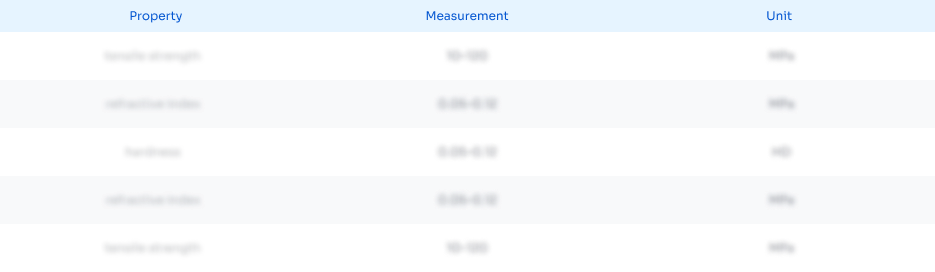
Abstract
Description
Claims
Application Information

- R&D
- Intellectual Property
- Life Sciences
- Materials
- Tech Scout
- Unparalleled Data Quality
- Higher Quality Content
- 60% Fewer Hallucinations
Browse by: Latest US Patents, China's latest patents, Technical Efficacy Thesaurus, Application Domain, Technology Topic, Popular Technical Reports.
© 2025 PatSnap. All rights reserved.Legal|Privacy policy|Modern Slavery Act Transparency Statement|Sitemap|About US| Contact US: help@patsnap.com