Metallographical corrosive for observing delta-Ni3Nb phase in ferronickel-based superalloy structure and using method of metallographical corrosive
A high-temperature alloy, nickel-iron-based technology, applied in the field of high-temperature alloy materials, can solve the problems of inability to develop the delta phase, poor corrosion uniformity of the substrate, etc., and achieve the effects of clear appearance, large contrast, and good chemical stability.
- Summary
- Abstract
- Description
- Claims
- Application Information
AI Technical Summary
Problems solved by technology
Method used
Image
Examples
Embodiment 1
[0028] The nickel-iron-based superalloy GH4169 alloy was corroded. The alloy uses γ' and γ″ / δ phases as high-temperature strengthening phases. The content of Fe in the alloy is 18-19% (mass fraction), and the content of Nb is 5.0-5.5% (mass fraction). The γ″ obtained by aging treatment -Ni 3 Nb transforms into its thermodynamically stable state δ-Ni during long-term (service) use 3 Nb phase, and aggregated to grow. figure 1 and figure 2 In order to use this corrosive agent to corrode the metallographic surface after long-term (service) mechanical polishing of GH4169 alloy, the (long) needle-shaped δ-Ni 3 The Nb phase is clearly visible; at the same time, the intragranular spherical γ' phase and the precipitated carbides at the grain boundaries are also clearly visible under the scanning electron microscope.
Embodiment 2
[0030] The IN718 alloy has been corroded, such as image 3 shown. After low-temperature aging treatment of IN718 alloy (the chemical composition is basically the same as that of GH4169 alloy), a small amount of δ-Ni is precipitated at the grain boundary 3 Nb phase, due to δ-Ni 3 The Nb phase has a small amount of precipitation and a small size, and is distributed in the grain boundary, so it is extremely difficult to observe. After using this etchant to corrode the mechanically polished metallographic surface, a small amount of (short) acicular δ-Ni distributed perpendicular to the grain boundaries can be clearly observed by scanning electron microscope 3 Nb phase.
PUM
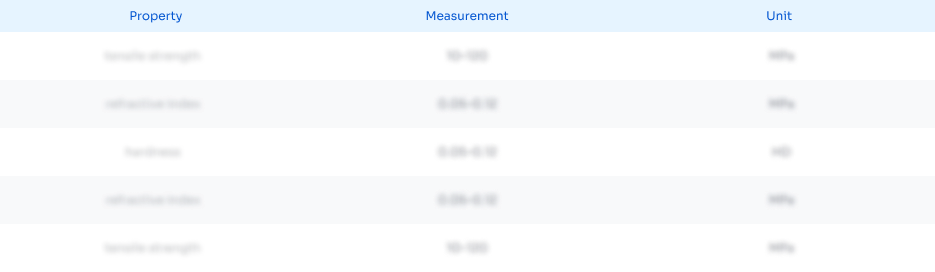
Abstract
Description
Claims
Application Information

- R&D
- Intellectual Property
- Life Sciences
- Materials
- Tech Scout
- Unparalleled Data Quality
- Higher Quality Content
- 60% Fewer Hallucinations
Browse by: Latest US Patents, China's latest patents, Technical Efficacy Thesaurus, Application Domain, Technology Topic, Popular Technical Reports.
© 2025 PatSnap. All rights reserved.Legal|Privacy policy|Modern Slavery Act Transparency Statement|Sitemap|About US| Contact US: help@patsnap.com