Anti-cracking PU white undercoat and preparation process thereof
A white primer and anti-cracking technology, applied in primers, coatings, polyurea/polyurethane coatings, etc., can solve the problems of shortening the service life of PU white primer, cracking of PU white primer, and affecting the appearance of furniture, etc., to achieve Effects of preventing cracking, improving flexibility, and promoting resin reaction
- Summary
- Abstract
- Description
- Claims
- Application Information
AI Technical Summary
Problems solved by technology
Method used
Image
Examples
Embodiment 1
[0020] Add 35 parts of modified synthetic fat resin, 7 parts of organic bentonite slurry, 1 part of modified adhesion aid, and 0.1 part of defoamer into the dispersion tank in turn, adjust the speed to 1000r / min, and disperse for 5min, wait for the above After the components are evenly dispersed, add 13 parts of rutile titanium dioxide, adjust the rotation speed to 1500r / min, disperse for 18 minutes, then keep the rotation speed constant, add 2.5 parts of zinc stearate, 35 parts of special paint powder, and the special Paint powder is a mixture of calcium carbonate and magnesium silicate, 5 parts of talcum powder, and disperse for 10 minutes. Finally, adjust the rotation speed to 1000r / min, and add 0.1 parts of leveling agent, 3.1 parts of sec-butyl ester, and 0.2 parts of time delay agent in turn. , the delay agent is a sodium compound, and disperse for 5 minutes.
Embodiment 2
[0022] Add 38 parts of modified synthetic fat resin, 7 parts of organic bentonite slurry, 2 parts of modified adhesion aid, and 0.1 part of defoamer into the dispersion tank in sequence, adjust the speed to 1000r / min, and disperse for 6 minutes, and wait for the above After the components are evenly dispersed, add 13 parts of rutile titanium dioxide, adjust the speed to 1500r / min, disperse for 20 minutes, then keep the speed constant, add 2.5 parts of zinc stearate, 30 parts of special paint powder, and the special Paint powder is a mixture of calcium carbonate and magnesium silicate, 5 parts of talcum powder, and disperse for 10 minutes. Finally, adjust the rotation speed to 1000r / min, and add 0.1 parts of leveling agent, 3.1 parts of sec-butyl ester, and 0.2 parts of time delay agent in turn. , the delay agent is a sodium compound, and disperse for 5 minutes.
Embodiment 3
[0024] Add 32 parts of modified synthetic fat resin, 7 parts of organic bentonite slurry, 1 part of modified adhesion aid, and 0.1 part of defoamer into the dispersion tank in sequence, adjust the speed to 1000r / min, and disperse for 8 minutes, and wait for the above After the components are evenly dispersed, add 13 parts of rutile titanium dioxide, adjust the rotation speed to 1500r / min, disperse for 15 minutes, then keep the rotation speed constant, add 2.5 parts of zinc stearate, 36 parts of special paint powder, and the special Paint powder is a mixture of calcium carbonate and magnesium silicate, 5 parts of talcum powder, and disperse for 10 minutes. Finally, adjust the rotation speed to 1000r / min, and add 0.1 parts of leveling agent, 3.1 parts of sec-butyl ester, and 0.2 parts of time delay agent in turn. , the delay agent is a sodium compound, and disperse for 5 minutes.
[0025] With the PU white primer sample that above-mentioned embodiment obtains, do relevant perfor...
PUM
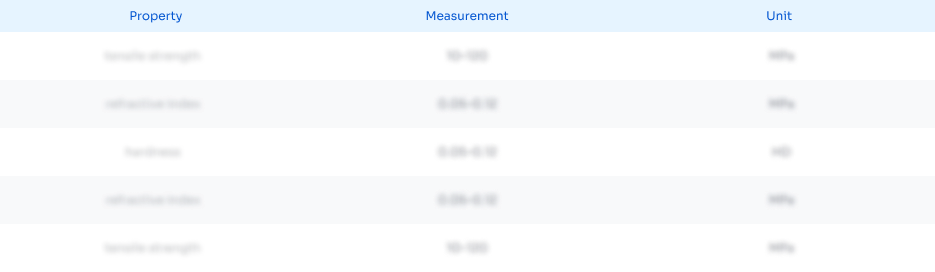
Abstract
Description
Claims
Application Information

- R&D
- Intellectual Property
- Life Sciences
- Materials
- Tech Scout
- Unparalleled Data Quality
- Higher Quality Content
- 60% Fewer Hallucinations
Browse by: Latest US Patents, China's latest patents, Technical Efficacy Thesaurus, Application Domain, Technology Topic, Popular Technical Reports.
© 2025 PatSnap. All rights reserved.Legal|Privacy policy|Modern Slavery Act Transparency Statement|Sitemap|About US| Contact US: help@patsnap.com