Enrichment and recovery method of carbon dioxide in iron ore sintering flue gas
A technology for sintering flue gas and carbon dioxide, which is applied in chemical instruments and methods, separation methods, inorganic chemistry, etc. High separation efficiency and zero discharge effect
- Summary
- Abstract
- Description
- Claims
- Application Information
AI Technical Summary
Problems solved by technology
Method used
Image
Examples
Embodiment 1
[0024] Raw material conditions for sintering: batching according to the mass ratio of mixed iron ore 61.41%, dolomite 5.61%, limestone 2.05%, quicklime 3.85%, sintering return ore 23.08%, coke powder 4.00% (the main chemical composition of the obtained sinter is: TFe58. 33%, SiO25.0%, R1.9, MgO2.3%). The above-mentioned sintering raw materials are distributed into the sintering machine 1 through the distributing device 2 for sintering.
[0025] The head flue gas accounting for 50% of the total volume of the flue gas is exported to the second condensing device 13 to condense and remove part of the water vapor, and then merge with the tail flue gas accounting for 20% of the total volume of the flue gas to form a circulating flue gas. Through the second dust remover 14 and the second exhaust fan 15 in turn, it is passed into the fume hood 4 completely covering the sintering machine 1, and industrial pure oxygen is mixed into the fume hood 4. The temperature and the volume concen...
Embodiment 2
[0027] Raw material conditions for sintering: batching according to the mass ratio of mixed iron ore 61.22%, dolomite 5.01%, limestone 2.33%, quicklime 4.51%, sintering return ore 23.08%, coke powder 3.85% (the main chemical composition of the obtained sinter is: TFe57. 7%, SiO24.9%, R2.0, MgO1.8%). The above-mentioned sintering raw materials are distributed into the sintering machine 1 through the distributing device 2 for sintering.
[0028] After leading out the head flue gas accounting for 55% of the total flue gas volume, it first passes through the second condensing device 13 to condense and remove part of the water vapor, and then merges with the tail flue gas accounting for 25% of the total flue gas volume to form circulating flue gas. The gas passes through the second dust remover 14 and the second exhaust fan 15 in turn into the fume hood 4 that completely covers the sintering machine 1, and industrial pure oxygen is mixed into the fume hood 4, and at the same time, ...
PUM
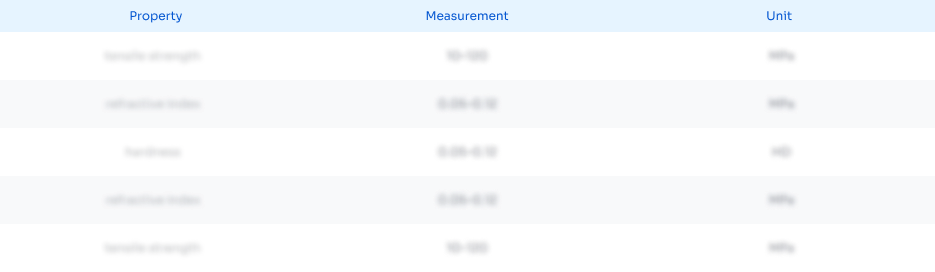
Abstract
Description
Claims
Application Information

- R&D
- Intellectual Property
- Life Sciences
- Materials
- Tech Scout
- Unparalleled Data Quality
- Higher Quality Content
- 60% Fewer Hallucinations
Browse by: Latest US Patents, China's latest patents, Technical Efficacy Thesaurus, Application Domain, Technology Topic, Popular Technical Reports.
© 2025 PatSnap. All rights reserved.Legal|Privacy policy|Modern Slavery Act Transparency Statement|Sitemap|About US| Contact US: help@patsnap.com