Heat treatment method for one-piece casting hot-rolled strip supporting roller
A heat treatment method and integral casting technology, applied in the field of heat treatment of rolls, can solve the problems of wear resistance, hardness drop that cannot meet the requirements of use, short service life of casting backup rolls, high production costs, etc. Accident capability, improved quality, effect of fine grains
- Summary
- Abstract
- Description
- Claims
- Application Information
AI Technical Summary
Problems solved by technology
Method used
Image
Examples
Embodiment Construction
[0018] The equipment and tooling hangers required by the present invention include: 1200°C high-temperature trolley-type resistance furnace, 750°C trolley-type resistance furnace, open-close type gas differential temperature furnace, high-pressure atomization spray quenching machine, lifting equipment, spreader, measuring temperature device, etc.
[0019] The processing steps of differential temperature heat treatment method of the present invention are as follows:
[0020] a. Process preparation: After rough machining of integrally cast hot-rolled strip support rolls, the roll neck is covered with thermal insulation material asbestos fiber felt, the roll body is pressed with armored thermocouples, externally connected with temperature control instruments, and hoisted to the trolley-type resistance The furnace support pad is firm to prevent deformation.
[0021] The role of asbestos fiber felt, which is a thermal insulation material for roll neck coating, is to prevent the ro...
PUM
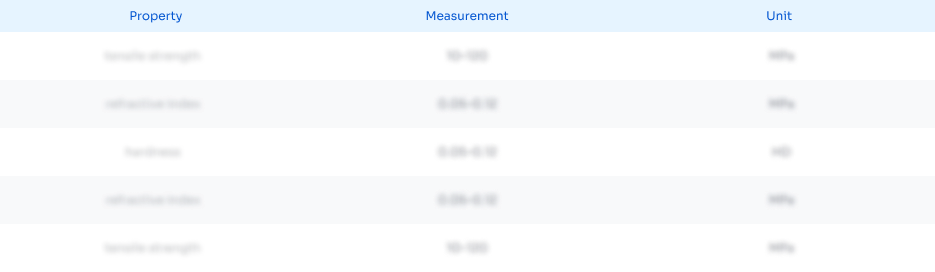
Abstract
Description
Claims
Application Information

- Generate Ideas
- Intellectual Property
- Life Sciences
- Materials
- Tech Scout
- Unparalleled Data Quality
- Higher Quality Content
- 60% Fewer Hallucinations
Browse by: Latest US Patents, China's latest patents, Technical Efficacy Thesaurus, Application Domain, Technology Topic, Popular Technical Reports.
© 2025 PatSnap. All rights reserved.Legal|Privacy policy|Modern Slavery Act Transparency Statement|Sitemap|About US| Contact US: help@patsnap.com