A method for comprehensive utilization of cyanide tailings cleaning transformation
A cyanide tailings and cleaning technology, applied in the direction of solid waste removal, etc., can solve the problems of unrecyclable, cyanide tailings pollution of the environment, etc., achieve good cyanide removal effect, solve backlog and secondary pollution , The effect of not polluting the environment
- Summary
- Abstract
- Description
- Claims
- Application Information
AI Technical Summary
Problems solved by technology
Method used
Image
Examples
Embodiment 1
[0037] A method for cleaning, transforming and comprehensively utilizing cyanide tailings, comprising the following steps:
[0038] 1) Using autoclaved method to hydrolyze cyanide in cyanide tailings
[0039] After the cyanide tailings are press-filtered, install them in a bucket truck, then put the bucket truck into the autoclave, vacuumize it for 0.4 hours after sealing, and then introduce steam. After the temperature rises to 170°C, start to hold the pressure for 4 hours , and then reduce the pressure to discharge ammonia-containing steam water, and the remaining secondary resource cyanide tailings in the autoclave;
[0040] 2) Add sodium dihydrogen phosphate and magnesium chloride to the ammonia-containing steam water obtained in 1), so that NH4 + , Mg 2+ and PO4 -3 The molar ratio is n(NH4 + ): n (Mg 2+ ): n(PO4 -3 )=1:1.1:1, adjust the pH to 8.5, use magnesium ammonium phosphate precipitation method to process the steam water containing ammonia nitrogen, then preci...
Embodiment 2
[0044] A method for cleaning, transforming and comprehensively utilizing cyanide tailings, comprising the following steps:
[0045] 1) Using autoclaved method to hydrolyze cyanide in cyanide tailings
[0046] After the cyanide tailings are press-filtered, install them in a bucket truck, then put the bucket truck into the autoclave, seal it and vacuumize it for 0.5 hours, then put in steam, and after the temperature rises to 190°C, start to hold the pressure for 2 hours , and then reduce the pressure to discharge ammonia-containing steam water, and the remaining secondary resource cyanide tailings in the autoclave;
[0047] 2) Add sodium dihydrogen phosphate and magnesium chloride to the ammonia-containing steam water obtained in 1), so that NH4 + , Mg 2+ and PO4 -3 The molar ratio is n(NH4 + ): n (Mg 2+ ): n(PO4 -3 )=1:1.1:1, adjust the pH to be 9, use magnesium ammonium phosphate precipitation method to process the steam water containing ammonia nitrogen, then precipita...
Embodiment 3
[0051] A method for cleaning, transforming and comprehensively utilizing cyanide tailings, comprising the following steps:
[0052] 1) Using autoclaved method to hydrolyze cyanide in cyanide tailings
[0053] Press-filter the cyanidation tailings and install them with a truck, then put the truck into the autoclave, seal it and vacuumize it for 1 hour, then introduce steam, and after the temperature rises to 200°C, start to hold the pressure for 1.5 hours , and then reduce the pressure to discharge ammonia-containing steam water, and the remaining secondary resource cyanide tailings in the autoclave;
[0054] 2) Add sodium dihydrogen phosphate and magnesium chloride to the ammonia-containing steam water obtained in 1), so that NH4 + , Mg 2+ and PO4 -3 The molar ratio is n(NH4 + ): n (Mg 2+ ): n(PO4 -3 )=1:1.1:1, adjust the pH to 9.5, use the magnesium ammonium phosphate precipitation method to treat the steam water containing ammonia nitrogen, then precipitate and filter ...
PUM
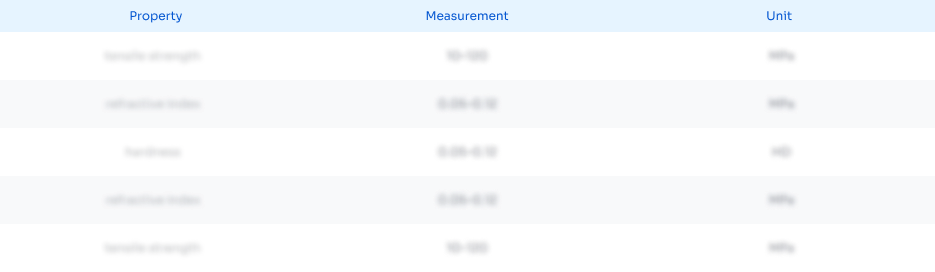
Abstract
Description
Claims
Application Information

- Generate Ideas
- Intellectual Property
- Life Sciences
- Materials
- Tech Scout
- Unparalleled Data Quality
- Higher Quality Content
- 60% Fewer Hallucinations
Browse by: Latest US Patents, China's latest patents, Technical Efficacy Thesaurus, Application Domain, Technology Topic, Popular Technical Reports.
© 2025 PatSnap. All rights reserved.Legal|Privacy policy|Modern Slavery Act Transparency Statement|Sitemap|About US| Contact US: help@patsnap.com