Method for preparing vanadium-nitrogen alloy
A technology of vanadium nitrogen alloy and vanadium oxide, which is applied in the field of designing and using iron powder as a catalyst to prepare vanadium nitrogen alloy, can solve the problems of low production yield and purity, achieve the effect of improving purity, reducing excessive reaction problems, and increasing speed
- Summary
- Abstract
- Description
- Claims
- Application Information
AI Technical Summary
Problems solved by technology
Method used
Examples
Embodiment 1
[0014] Mix vanadium oxide (vanadium pentoxide, vanadium tetroxide, vanadium trioxide or a mixture of the three), graphite powder and iron powder evenly, and the iron powder accounts for 0.3% of the total mass. The above mixture is pressed in a ball press to obtain spherical raw meal. Put the raw material into the sintering furnace. The sintering process of the sintering furnace is as follows: 6 hours from normal temperature to 1300 ℃, and keep at the highest temperature for 4 hours; ensure that the furnace is filled with nitrogen during the sintering process. After the sintering is completed and the furnace cools down naturally, the product is sintered. Wherein, in the finally obtained vanadium-nitrogen alloy, the proportion of vanadium element and nitrogen element is 98.9%, and the content of other elements is relatively small.
Embodiment 2
[0016] Mix vanadium oxide (vanadium pentoxide, vanadium tetroxide, vanadium trioxide or a mixture of the three), graphite powder and iron powder evenly, and the iron powder accounts for 1% of the total mass. The above mixture is pressed in a ball press to obtain spherical raw meal. Put the raw material into the sintering furnace. The sintering process of the sintering furnace is as follows: 6 hours from normal temperature to 1400 ℃, and keep at the highest temperature for 2 hours; ensure that the furnace is filled with nitrogen during the sintering process. After the sintering is completed and the furnace cools down naturally, the product is sintered. Wherein, in the finally obtained vanadium-nitrogen alloy, the proportion of vanadium element and nitrogen element is 98.8%, and the content of other elements is relatively small.
Embodiment 3
[0018] Mix vanadium oxide (vanadium pentoxide, vanadium tetroxide, vanadium trioxide or a mixture of the three), graphite powder and iron powder evenly, and the iron powder accounts for 0.8% of the total mass. The above mixture is pressed in a ball press to obtain spherical raw meal. Put the raw material into the sintering furnace. The sintering process of the sintering furnace is as follows: 6 hours from normal temperature to 1500 ℃, and keep at the highest temperature for 3 hours; ensure that the furnace is filled with nitrogen during the sintering process. After the sintering is completed and the furnace cools down naturally, the product is sintered. Wherein, in the finally obtained vanadium-nitrogen alloy, the proportion of vanadium element and nitrogen element is 99.0%, and the content of other elements is relatively small.
PUM
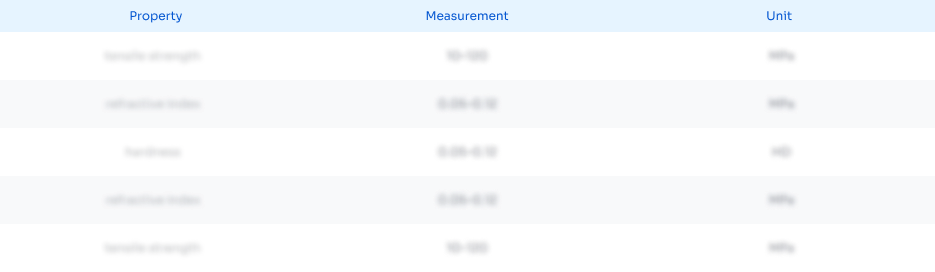
Abstract
Description
Claims
Application Information

- R&D
- Intellectual Property
- Life Sciences
- Materials
- Tech Scout
- Unparalleled Data Quality
- Higher Quality Content
- 60% Fewer Hallucinations
Browse by: Latest US Patents, China's latest patents, Technical Efficacy Thesaurus, Application Domain, Technology Topic, Popular Technical Reports.
© 2025 PatSnap. All rights reserved.Legal|Privacy policy|Modern Slavery Act Transparency Statement|Sitemap|About US| Contact US: help@patsnap.com