Method for preparing charcoal from sheep manure and wood dust
A technology of wood chips and sheep manure, which is applied in special forms of dry distillation, petroleum industry, biofuel, etc., can solve the problems that manure cannot be effectively treated, trees cannot be regenerated, and it is difficult to meet the national charcoal quality standards
- Summary
- Abstract
- Description
- Claims
- Application Information
AI Technical Summary
Problems solved by technology
Method used
Image
Examples
Embodiment 1
[0015] Embodiment 1: the method that utilizes sheep manure and sawdust to prepare charcoal is the following steps
[0016] a. After cleaning, air-drying, crushing and crushing, 50 parts of sheep manure are mixed with 50 parts of sawdust and then sent to the dryer for drying. The sawdust is preferably sawdust. The temperature of the dryer is 160°C and the drying time is The moisture content of the raw materials exported by the dryer is 8%;
[0017] b. The raw material obtained in step a is fed into a rod-making machine, and the rod-making machine is pressed at a temperature of 260° C. to obtain a columnar semi-finished product with a length of 30 cm, a smooth surface and no obvious cracks for use;
[0018] c. The columnar semi-finished product obtained in step b is put into a carbonization kiln for carbonization. The height of the columnar semi-finished product is 50 cm from the ground, the burning time is 3 days, and the kiln is sealed when the temperature reaches 800 ° C. ...
Embodiment 2
[0019] Embodiment 2: the method that utilizes sheep manure and sawdust to prepare charcoal is the following steps
[0020] a. After washing, air-drying, crushing and crushing, 60 parts of sheep manure are mixed with 40 parts of sawdust and then sent to the dryer for drying. The sawdust is preferably sawdust. The temperature of the dryer is 220°C, and the drying time is The moisture content of the raw materials exported by the dryer is 10%;
[0021] b. The raw material obtained in step a is sent to a rod making machine, and the rod making machine is pressed at a temperature of 300°C to obtain a columnar semi-finished product with a length of 30 cm, a smooth surface and no obvious cracks for use;
[0022] c. Put the columnar semi-finished product obtained in step b into a carbonization kiln for carbonization. The height of the columnar semi-finished product is 80 cm from the ground. The burning time is 4 days. When the temperature reaches 800 ° C, the kiln is closed. After na...
Embodiment 3
[0023] Embodiment 3: the method that utilizes sheep manure and sawdust to prepare charcoal is the following steps
[0024] a. 70 parts of sheep manure is washed, air-dried, crushed and mixed with 30 parts of wood chips, and then sent to the dryer for drying. The wood chips are preferably sawdust. The temperature of the dryer is 200 ° C, and the drying time is The moisture content of the raw materials exported by the dryer is 10%;
[0025] b. The raw material obtained in step a is sent to a rod making machine, and the rod making machine is pressed at a temperature of 280°C to obtain a columnar semi-finished product with a length of 3-40 cm, a smooth surface and no obvious cracks for use;
[0026] c. The columnar semi-finished product obtained in step b is put into a carbonization kiln for carbonization. The height of the columnar semi-finished product is 70 cm from the ground, the burning time is 3 days, and the kiln is sealed when the temperature reaches 500 ° C. The finish...
PUM
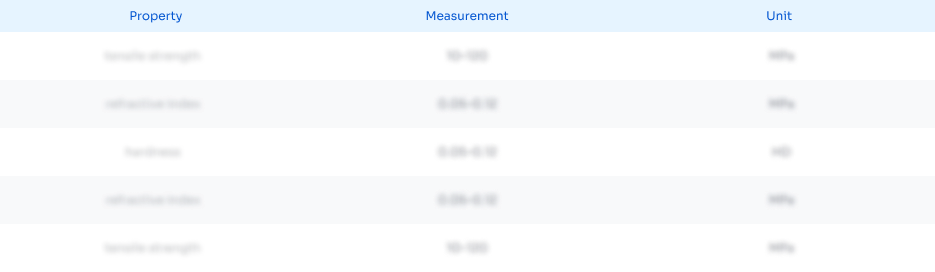
Abstract
Description
Claims
Application Information

- Generate Ideas
- Intellectual Property
- Life Sciences
- Materials
- Tech Scout
- Unparalleled Data Quality
- Higher Quality Content
- 60% Fewer Hallucinations
Browse by: Latest US Patents, China's latest patents, Technical Efficacy Thesaurus, Application Domain, Technology Topic, Popular Technical Reports.
© 2025 PatSnap. All rights reserved.Legal|Privacy policy|Modern Slavery Act Transparency Statement|Sitemap|About US| Contact US: help@patsnap.com