Preparation method of LED light source and preparation method of LED light-emitting module
A technology of LED light source and LED chip, applied in the direction of light source, electric light source, point light source, etc., can solve the problems of high material cost, time cost and labor cost, influence of lighting angle, etc., to reduce the speed of light decay and production cycle. and time cost, the effect of reducing cost
- Summary
- Abstract
- Description
- Claims
- Application Information
AI Technical Summary
Problems solved by technology
Method used
Image
Examples
Embodiment 1
[0049] (1) The LED chip is a flip-chip blue LED chip, which is bonded to the PET film with UV glue on the surface at an equidistant distribution. The thickness of the film is 0.75mm, and the ultraviolet light is initially cured for 8s;
[0050] (2) On the surface of the LED chip (the main light-emitting surface and the four sides), spray a layer of organic silica gel water with a refractive index n=1.56, which is added with SiO with an average particle size of 10nm 2 particles, the SiO 2 Mass occupancy of particles in silicone water and SiO 2 7.5% of the total mass of the particles, the thickness of spraying is 0.5mm, and then placed in a 100°C oven for 25min pre-curing to prepare the isolation adhesive layer;
[0051] (3) Take out and spray a layer of silicone water mixed with fluorescent powder with a refractive index n=1.45. The silicone water mixed with fluorescent powder is composed of fluorescent powder (yellow fluorescent powder) and silicone water. The quality of the ...
Embodiment 2
[0057] Arrange the LED white light sources prepared in Example 1 above in a series-parallel manner, and solder them on the PCB with solder paste to obtain an LED white light emitting module.
[0058] Such as image 3 As shown, the LED white light source 4 is soldered on the substrate 5 in series.
Embodiment 3
[0060] (1) The LED chip is a flip-chip blue LED chip, which is bonded to the PTFE film with UV glue on the surface at an equidistant distribution. The thickness of the film is 1.2mm, and the ultraviolet light is initially cured for 15s;
[0061] (2) On the surface of the LED chip (the main light-emitting surface and the four sides), spray a layer of organic silica gel water with a refractive index n=1.55, which is added with SiO with an average particle size of 15nm 2 particles, the SiO 2 Mass occupancy of particles in silicone water and SiO 2 10% of the total mass of the particles, the thickness of spraying is 0.6mm, and then placed in a 100°C oven for 35min pre-curing;
[0062] (3) Take out and spray a layer of silicone water mixed with fluorescent powder with a refractive index n=1.42. The silicone water mixed with fluorescent powder is composed of fluorescent powder (yellow fluorescent powder) and silicone water. The quality of the fluorescent powder is 100%. The compone...
PUM
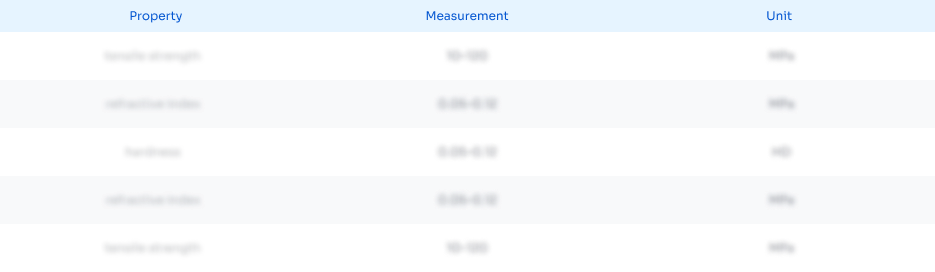
Abstract
Description
Claims
Application Information

- R&D
- Intellectual Property
- Life Sciences
- Materials
- Tech Scout
- Unparalleled Data Quality
- Higher Quality Content
- 60% Fewer Hallucinations
Browse by: Latest US Patents, China's latest patents, Technical Efficacy Thesaurus, Application Domain, Technology Topic, Popular Technical Reports.
© 2025 PatSnap. All rights reserved.Legal|Privacy policy|Modern Slavery Act Transparency Statement|Sitemap|About US| Contact US: help@patsnap.com