Method for realizing thermal compensation of lead screw of numerical control machine tool
A technology of numerical control machine tools and implementation methods, applied in the directions of digital control, program control, electrical program control, etc., can solve the problems of ball screw thermal compensation accuracy drop, achieve lower accuracy requirements, improve thermal compensation accuracy and stability, reduce The effect of non-linear error
- Summary
- Abstract
- Description
- Claims
- Application Information
AI Technical Summary
Problems solved by technology
Method used
Image
Examples
Embodiment 1
[0034] The invention provides a method for realizing thermal compensation of a lead screw of a numerically controlled machine tool, the steps of which are as follows:
[0035] a. Detect the thermal deformation of the screw of each linear axis of the machine tool, and divide it into several stages from 0 to the maximum deformation;
[0036] b. Divide the lead screw thermal compensation section corresponding to the machine tool coordinates, and set a compensation point for each section;
[0037] c. Detect the positioning accuracy error of each section of the corresponding coordinate axis of the machine tool when the lead screw of each linear axis of the machine tool is thermally deformed at each level;
[0038] d. Establish a thermal compensation database for machine tool screw;
[0039] e. Develop a thermal compensation controller to convert each level of thermal deformation of the lead screw into a corresponding thermal compensation control code;
[0040] f. According to the...
Embodiment 2
[0042]On the basis of embodiment 1, the best implementation mode of the present invention is:
[0043] The thermal deformation of each linear axis screw of the machine tool is detected by using a non-contact displacement sensor (such as: eddy current displacement sensor, capacitive displacement sensor, etc.), on the end surface of the non-motor connection end (floating end) of the machine tool screw , direct real-time detection of the thermal deformation of the lead screws of each linear axis of the machine tool. And the thermal deformation of each linear axis lead screw of the machine tool, from 0 to the maximum value, is divided into several grades according to the accuracy requirements of the machine tool after compensation.
[0044] The division of the lead screw thermal compensation section corresponding to the coordinates of the machine tool is to divide the entire stroke of each linear axis of the machine tool into several sections, and each section corresponds to a com...
PUM
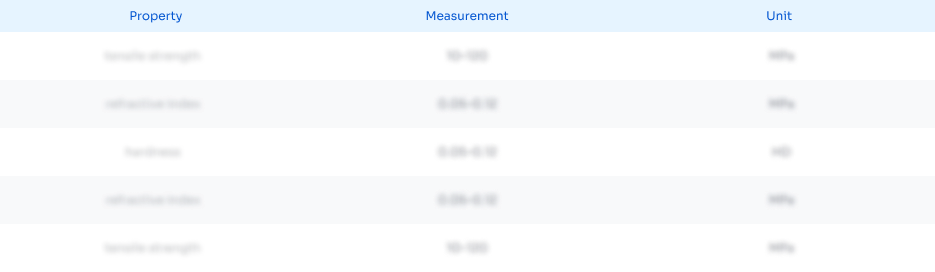
Abstract
Description
Claims
Application Information

- R&D
- Intellectual Property
- Life Sciences
- Materials
- Tech Scout
- Unparalleled Data Quality
- Higher Quality Content
- 60% Fewer Hallucinations
Browse by: Latest US Patents, China's latest patents, Technical Efficacy Thesaurus, Application Domain, Technology Topic, Popular Technical Reports.
© 2025 PatSnap. All rights reserved.Legal|Privacy policy|Modern Slavery Act Transparency Statement|Sitemap|About US| Contact US: help@patsnap.com