Load observer-based virtual line shaft control method for multiple permanent magnet synchronous motors
A permanent magnet synchronous motor, load observer technology, applied in multiple motor speed/torque control, motor generator control, electronic commutation motor control, etc. And other issues
- Summary
- Abstract
- Description
- Claims
- Application Information
AI Technical Summary
Problems solved by technology
Method used
Image
Examples
Embodiment Construction
[0058] In the present invention, the observed load torque is fed back to the virtual master shaft as the feedback torque, thereby coordinating the synchronous operation among the slave shafts, and more truly reflecting the dynamic relationship between the shafts, and at the same time, further improving the robustness of the system. Sticky, which feeds forward the load torque observations to the current loop of the slave axis motor.
[0059] Sliding-mode variable structure control (sliding-mode variable structure control, SMC) can overcome the uncertainty of the system, and has the advantages of strong robustness to disturbance and unmodeled systems, so the present invention applies the exponential reaching law algorithm In the load observer design section.
[0060] The technical scheme adopted by the present invention is based on the virtual main shaft control of multi-permanent-magnet synchronous motors based on load observers, including the following aspects:
[0061] (1) T...
PUM
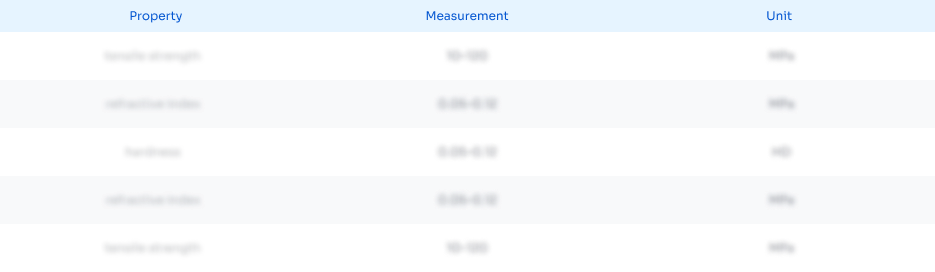
Abstract
Description
Claims
Application Information

- R&D
- Intellectual Property
- Life Sciences
- Materials
- Tech Scout
- Unparalleled Data Quality
- Higher Quality Content
- 60% Fewer Hallucinations
Browse by: Latest US Patents, China's latest patents, Technical Efficacy Thesaurus, Application Domain, Technology Topic, Popular Technical Reports.
© 2025 PatSnap. All rights reserved.Legal|Privacy policy|Modern Slavery Act Transparency Statement|Sitemap|About US| Contact US: help@patsnap.com