Preparation method of PVDF (polyvinylidene fluoride) mixture lithium-ion battery separator
A lithium-ion battery, polyvinylidene fluoride technology, applied in battery pack parts, circuits, electrical components, etc., can solve the problems of uneven micropore diameter of diaphragm, poor mechanical performance of diaphragm, low ionic conductivity, etc. Physical and electrochemical properties cannot be achieved simultaneously, parameters are easy to control, and the preparation process is simple.
- Summary
- Abstract
- Description
- Claims
- Application Information
AI Technical Summary
Problems solved by technology
Method used
Image
Examples
Embodiment 1
[0029] (1) Selection of solvent: The solvent is DMAc.
[0030] (2) Preparation of the original casting solution: first measure 76.2g of DMAc, add the pore-forming agent PVP at a mass percentage of 4.0 to form a mixed solution, then add PVDF at a mass percentage of 15.0, and then add HDPE and PSF at a mass percentage of 1.4 And 3.4 mass percent is added.
[0031] (3) Preparation of homogeneous casting solution: heat the original casting solution in a heater at 65°C for 7 hours, then stir with a magnetic stirrer, stir for 2 hours and then let it stand for 24 hours defoaming.
[0032] (4) Basement film casting: Cast the obtained homogeneous casting film on a clean and smooth glass plate after drying with absorbent cotton, and adjust the scraper parameters to scrape the film.
[0033] (5) Phase separation: The film obtained after scraping was immersed in deionized water for phase separation to form pores and left for 24 hours.
[0034] (6) Membrane drying: After standing still,...
Embodiment 2
[0036] (1) Selection of solvent: The solvent is DMAc.
[0037] (2) Preparation of the original casting solution: first measure 86.2g of DMAc, add the pore-forming agent PVP at a mass percentage of 1.0 to form a mixed solution, then add PVDF at a mass percentage of 10.0, and then add HDPE and PSF at a mass percentage of 1.2 And 1.6 mass percent is added.
[0038] (3) Preparation of homogeneous casting solution: heat the original casting solution in a heater at 78°C for 5 hours, then stir with a magnetic stirrer for 2.5 hours and then static for 24 hours. Set for defoaming.
[0039] (4) Basement film casting: Cast the obtained homogeneous casting film on a clean and smooth glass plate after drying with absorbent cotton, and adjust the scraper parameters to scrape the film.
[0040] (5) Phase separation: The film obtained after scraping was immersed in deionized water for phase separation to form pores and left for 24 hours.
[0041] (6) Membrane drying: After standing still, ...
Embodiment 3
[0043] (1) Selection of solvent: The solvent is DMF.
[0044] (2) Preparation of the original casting solution: first measure 80.2g of DMAc, add the pore-forming agent PVP at a mass percentage of 3.0 to form a mixed solution, then add PVDF at a mass percentage of 12.0, and then add HDPE and PSF at a mass percentage of 1.4 And 3.4 mass percent is added.
[0045] (3) Preparation of homogeneous casting solution: heat the original casting solution in a heater at a heating temperature of 70°C for 6 hours, then stir with a magnetic stirrer for 2.5 hours and then static for 24 hours. Set for defoaming.
[0046] (4) Casting of base film: cast the obtained homogeneous casting solution on a clean and smooth glass plate after drying with absorbent cotton, and adjust the parameters of the scraper to scrape the film.
[0047](5) Phase separation: The film obtained after scraping was immersed in deionized water for phase separation to form pores and left for 24 hours.
[0048] (6) Membra...
PUM
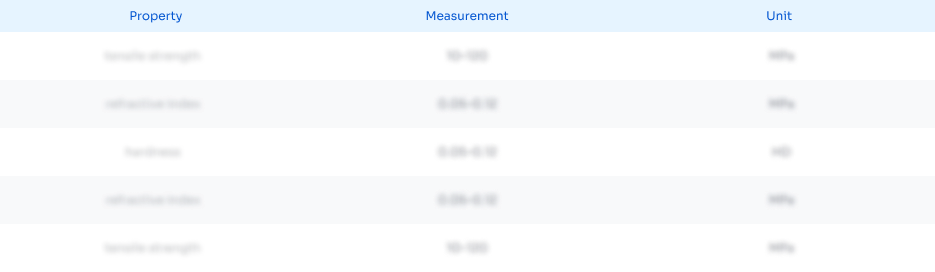
Abstract
Description
Claims
Application Information

- R&D
- Intellectual Property
- Life Sciences
- Materials
- Tech Scout
- Unparalleled Data Quality
- Higher Quality Content
- 60% Fewer Hallucinations
Browse by: Latest US Patents, China's latest patents, Technical Efficacy Thesaurus, Application Domain, Technology Topic, Popular Technical Reports.
© 2025 PatSnap. All rights reserved.Legal|Privacy policy|Modern Slavery Act Transparency Statement|Sitemap|About US| Contact US: help@patsnap.com