Preparation process of glass fiber composite material
A glass fiber and composite material technology, which is applied in the field of glass fiber composite material preparation technology, can solve problems such as poor performance of composite materials, and achieve the effects of increasing active groups, increasing compatibility, and increasing mechanical properties.
- Summary
- Abstract
- Description
- Claims
- Application Information
AI Technical Summary
Problems solved by technology
Method used
Examples
Embodiment 1
[0017] A kind of glass fiber composite material preparation process, its concrete steps are:
[0018] (1) Glass fiber high-temperature treatment process: put a certain amount of glass fiber into the muffle furnace, heat treatment in the muffle furnace at 400°C for 30 minutes, remove the moisture adsorbed on the surface of the glass fiber, take it out and seal it for later use;
[0019] (2) Acid-base etching treatment process: soak the above-mentioned treated glass fiber in 10% NaOH solution for 5 minutes, take it out and wash it with distilled water until neutral, then immerse the glass fiber in 1mol / L dilute HCl for 30 minutes, Take it out and wash it with distilled water until neutral, place it in an oven to dry at 80°C, and set aside;
[0020] (3) Silane coupling agent treatment process: Take the glass fiber after the above treatment, soak it in NaOH solution with a mass fraction of 5% for 5 minutes, take it out, wash it with distilled water until neutral, and take out the ...
Embodiment 2
[0024] A kind of glass fiber composite material preparation process, its concrete steps are:
[0025] (1) Glass fiber high-temperature treatment process: put a certain amount of glass fiber into the muffle furnace, heat treatment in the muffle furnace at 420°C for 35 minutes, remove the moisture adsorbed on the surface of the glass fiber, take it out and seal it for later use;
[0026] (2) Acid-base etching treatment process: soak the above-mentioned treated glass fiber in 12% NaOH solution for 7 minutes, take it out and wash it with distilled water until neutral, then immerse the glass fiber in 1.2mol / L dilute HCl for 35 minutes , take it out and wash it with distilled water until neutral, place it in an oven to dry at 90°C, and set aside;
[0027] (3) Silane coupling agent treatment process: Take the glass fiber after the above treatment, soak it in NaOH solution with a mass fraction of 7% for 5 minutes, take it out, wash it with distilled water until neutral, and take out t...
Embodiment 3
[0031] A kind of glass fiber composite material preparation process, its concrete steps are:
[0032] (1) Glass fiber high-temperature treatment process: put a certain amount of glass fiber into the muffle furnace, heat treatment in the muffle furnace at 450°C for 40 minutes, remove the moisture adsorbed on the surface of the glass fiber, take it out and seal it for later use;
[0033] (2) Acid-base etching treatment process: soak the above-mentioned treated glass fiber in 15% NaOH solution for 10 minutes, take it out and wash it with distilled water until neutral, then immerse the glass fiber in 1.5mol / L dilute HCl for 40 minutes , take it out and wash it with distilled water until neutral, place it in an oven to dry at 100°C, and set aside;
[0034] (3) Silane coupling agent treatment process: Take the glass fiber after the above treatment, soak it in NaOH solution with a mass fraction of 10% for 5 minutes, take it out, wash it with distilled water until neutral, and take ou...
PUM
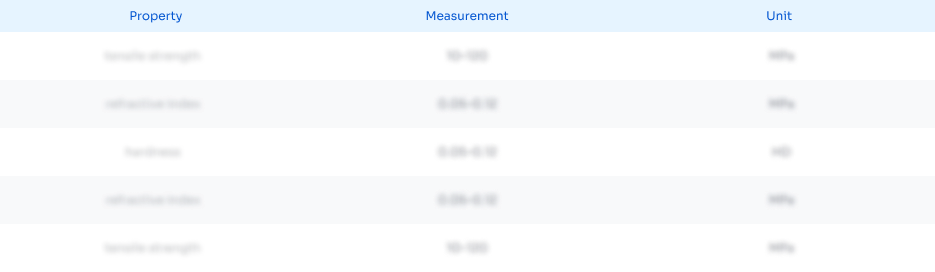
Abstract
Description
Claims
Application Information

- R&D
- Intellectual Property
- Life Sciences
- Materials
- Tech Scout
- Unparalleled Data Quality
- Higher Quality Content
- 60% Fewer Hallucinations
Browse by: Latest US Patents, China's latest patents, Technical Efficacy Thesaurus, Application Domain, Technology Topic, Popular Technical Reports.
© 2025 PatSnap. All rights reserved.Legal|Privacy policy|Modern Slavery Act Transparency Statement|Sitemap|About US| Contact US: help@patsnap.com