Dip coating treatment method for chemical fiber ropes
A treatment method and rope technology, applied in the direction of pretreatment surface, device for coating liquid on the surface, coating, etc., can solve the problems of large influence of weather factors, poor solution permeability, long curing time, etc., and achieve remarkable drawing effect , Improve the effect and efficiency, improve the effect of drying efficiency and effect
- Summary
- Abstract
- Description
- Claims
- Application Information
AI Technical Summary
Problems solved by technology
Method used
Examples
Embodiment 1
[0020] The dipping solution is mixed and diluted with water-based polyurethane and water at a weight ratio of 1:1. During the dipping process of the rope, an ultrasonic device is added to the bath to ultrasonically treat the rope in the bath. The purpose is to make the glue more uniform and sufficient. Dip into the rope. The impregnation process adopts a combination of turbo mechanical stirring and ultrasonic dispersion, the turbine speed is 30 rpm, continuous stirring; the ultrasonic frequency is 30000HZ, intermittent start, the time interval is 10s. Then, the rope is extruded through a grinding port less than 1mm in diameter of the rope to squeeze out excess rubber. Then enter the pre-drying method, using the microwave drying method, the microwave frequency is 2450MHZ±25MHZ, because the microwave does not directly heat the rope, but prefers to directly evaporate the moisture of the coating, and then infrared drying, irradiated by infrared lamps, the temperature is 55 ±5°C, ...
Embodiment 2
[0022] The dipping solution is mixed and diluted with water-based polyurethane and water at a weight ratio of 1:5. The dipping process uses a combination of turbo mechanical stirring and ultrasonic dispersion. The turbine speed is 40 rpm, continuous stirring; the ultrasonic frequency is 25000HZ, intermittent start , the time interval is 20s. Then, the rope is extruded through a grinding port less than 1mm in diameter of the rope to squeeze out excess rubber. Then enter the pre-drying method, using microwave drying method, the microwave frequency is 2450MHZ±25MHZ, then infrared drying, irradiated by infrared lamps, the temperature is 55±5°C, and then enter the drawing unit 1, after passing through the drawing unit 1 , enter the hot air oven, and carry out hot air circulation drying. The oven is equipped with three temperature-adjustable heating zones, and each zone is set with the best heating temperature and residence time. The maximum temperature range is 75±5°C. After the ro...
Embodiment 3
[0024] The dipping solution is mixed and diluted with water-based polyurethane and water at a weight ratio of 1:10. The dipping process adopts a combination of turbo mechanical stirring and ultrasonic dispersion. The turbine speed is 100 rpm, continuous stirring; the ultrasonic frequency is 20000HZ, intermittent start , the time interval is 50s. Then, the rope is extruded through a grinding port less than 1mm in diameter of the rope to squeeze out excess rubber. Then enter the pre-drying method, using microwave drying method, the microwave frequency is 2450MHZ±25MHZ, then infrared drying, irradiated by infrared lamps, the temperature is 55±5°C, and then enter the drawing unit 1, after passing through the drawing unit 1 , enter the hot air oven, and carry out hot air circulation drying. The oven is equipped with three temperature-adjustable heating zones, and each zone is set with the best heating temperature and residence time. The maximum temperature range is 75±5°C. After th...
PUM
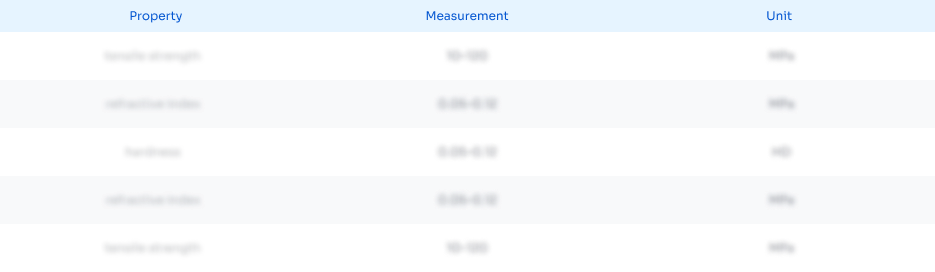
Abstract
Description
Claims
Application Information

- R&D
- Intellectual Property
- Life Sciences
- Materials
- Tech Scout
- Unparalleled Data Quality
- Higher Quality Content
- 60% Fewer Hallucinations
Browse by: Latest US Patents, China's latest patents, Technical Efficacy Thesaurus, Application Domain, Technology Topic, Popular Technical Reports.
© 2025 PatSnap. All rights reserved.Legal|Privacy policy|Modern Slavery Act Transparency Statement|Sitemap|About US| Contact US: help@patsnap.com