Method for recovering platinum from waste catalyst
A waste catalyst and abrasive technology, which is applied in the direction of improving process efficiency, can solve the problems of low cost, high reagent consumption, and low recovery rate, and achieve the effects of reducing the cost of three wastes treatment, reducing equipment loss, and reducing production costs
- Summary
- Abstract
- Description
- Claims
- Application Information
AI Technical Summary
Problems solved by technology
Method used
Examples
Embodiment 1
[0022] Grind the waste catalyst into fine particles, put the ground waste catalyst into a muffle furnace and roast for 1 hour at a temperature of 400°C. After cooling, mix the above-treated waste catalyst and abrasive sodium hydroxide into an autoclave Sealed wet grinding, the ratio of catalyst to grinding agent is 8:1, the wet grinding temperature is 150°C, and when the temperature reaches 140°C, oxygen is blown into the kettle. The wet-milled raw materials are vacuum filtered to separate the solid from the liquid, and the leaching residue and leaching liquid are put into an autoclave together. The leaching liquid is 5% NaCN solution, the leaching heating temperature is 140°C, and the pressure is 1.6 MPa. The leaching rate of platinum was 90%.
Embodiment 2
[0024] Grind the waste catalyst into fine particles, put the ground waste catalyst into a muffle furnace and roast for 1 hour at a temperature of 400°C. After cooling, mix the above-treated waste catalyst and abrasive sodium hydroxide into an autoclave Sealed wet grinding, the ratio of catalyst to grinding agent is 8:1, the wet grinding temperature is 170°C, and when the temperature reaches 160°C, oxygen is blown into the kettle. The wet-milled raw materials are vacuum filtered to separate the solid and liquid, and the leaching residue and leaching liquid are put into an autoclave together. The leaching liquid is 5% NaCN solution, the leaching heating temperature is 160°C, and the pressure is 2MPa. Measured after cooling The platinum leaching rate was 94%.
Embodiment 3
[0026] Grind the waste catalyst into fine particles, put the ground waste catalyst into a muffle furnace and roast for 1 hour at a temperature of 500°C. After cooling, mix the above-treated waste catalyst and abrasive sodium hydroxide into an autoclave Sealed wet grinding, the ratio of catalyst to grinding agent is 10:1, the wet grinding temperature is 200°C, and when the temperature reaches 170°C, oxygen is blown into the kettle. The wet-milled raw materials are vacuum filtered to separate the solid from the liquid, and the leaching residue and leaching liquid are put into an autoclave together. The leaching liquid is 7% NaCN solution. The leaching heating temperature is 140°C and the pressure is 1.6-2 MPa. The measured platinum leaching rate was 93%.
PUM
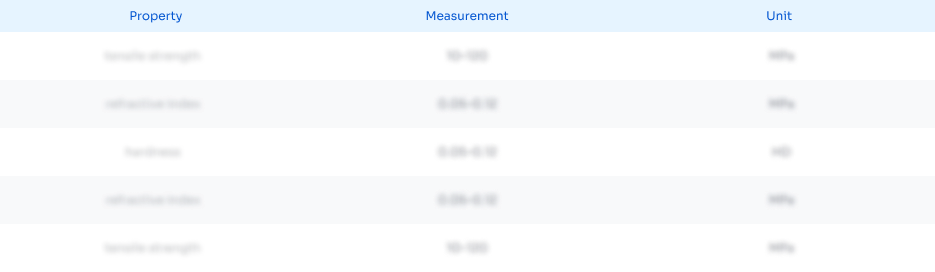
Abstract
Description
Claims
Application Information

- Generate Ideas
- Intellectual Property
- Life Sciences
- Materials
- Tech Scout
- Unparalleled Data Quality
- Higher Quality Content
- 60% Fewer Hallucinations
Browse by: Latest US Patents, China's latest patents, Technical Efficacy Thesaurus, Application Domain, Technology Topic, Popular Technical Reports.
© 2025 PatSnap. All rights reserved.Legal|Privacy policy|Modern Slavery Act Transparency Statement|Sitemap|About US| Contact US: help@patsnap.com