Direct torque control method for six-phase synchronous motor with zero-sequence current self-correction
A technology of direct torque control and zero-sequence current, applied in the field of multi-phase permanent magnet motor drive control, can solve the increase of low-order harmonic components of phase current, decrease of steady-state performance of direct torque control drive system, and decrease of load capacity And other issues
- Summary
- Abstract
- Description
- Claims
- Application Information
AI Technical Summary
Problems solved by technology
Method used
Image
Examples
Embodiment Construction
[0062] The present invention will be further described in conjunction with embodiment and accompanying drawing now.
[0063] In the embodiment of the present invention, the drive system hardware structure is as follows Figure 8 As shown, including: rectifier circuit, filter capacitor, six-phase inverter, permanent magnet synchronous motor with six-phase symmetrical winding biased at 60 degrees, six-phase winding current acquisition circuit, rotor position angle acquisition circuit, isolation drive, central controller, man-machine interface. A suitable DC power supply can also be used to provide the DC bus voltage of the three-phase inverter. The power tube in the inverter adopts IGBT or MOFET, and the central controller adopts DSP or single-chip microcomputer. The winding current acquisition circuit is formed by combining a Hall current sensor and an operational amplifier, or by combining a winding string power resistor followed by a differential operational amplifier. The...
PUM
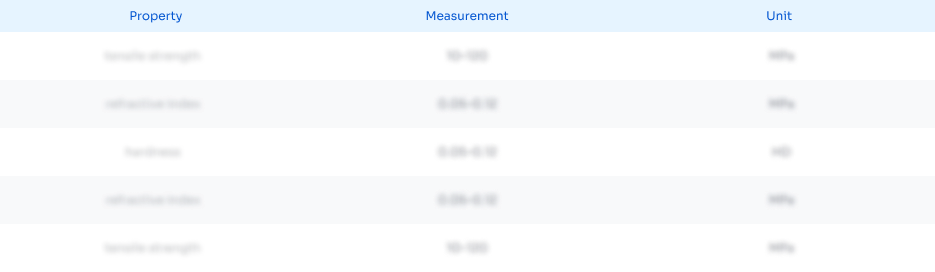
Abstract
Description
Claims
Application Information

- R&D
- Intellectual Property
- Life Sciences
- Materials
- Tech Scout
- Unparalleled Data Quality
- Higher Quality Content
- 60% Fewer Hallucinations
Browse by: Latest US Patents, China's latest patents, Technical Efficacy Thesaurus, Application Domain, Technology Topic, Popular Technical Reports.
© 2025 PatSnap. All rights reserved.Legal|Privacy policy|Modern Slavery Act Transparency Statement|Sitemap|About US| Contact US: help@patsnap.com