Processing process of wear-resisting anti-impact type pile foundation steel protective barrel
A processing technology, steel casing technology, applied in the direction of basic structure engineering, process efficiency improvement, metal material coating technology, etc., can solve the hidden dangers of engineering quality, affect the construction quality of pile foundation, rupture and scrapping and other problems, and achieve the elimination of safety Hidden dangers, saving scrap rate of consumables, and improving quality
- Summary
- Abstract
- Description
- Claims
- Application Information
AI Technical Summary
Problems solved by technology
Method used
Examples
Embodiment 1
[0031] This embodiment provides a processing technology for a wear-resistant and impact-resistant pile foundation steel casing. The chemical composition of the selected steel blank is: C: 0.26%, Si: 0.20%, Mn: 0.88%, Cr: 0.85% , Mo: 0.16%, N: 0.015%, P: 0.010%, S: 0.001%, Nb: 0.01%, V: 0.18%, rare earth: 0.22%, 0.4% residual elements, and the rest is Fe;
[0032] Among the rare earths, the following components are contained by weight percentage: Gd: 15%, Pr: 3%, Dy: 7%, Ac: 12.5%, Nd: 15%, Sm: 11%, and the balance is La;
[0033] Specifically include the following steps:
[0034] Step (1): Put the above-mentioned steel blank in a furnace and heat it to 1300-1400°C. After the steel blank is heated, it is drawn into a closed environment of methane or ethane for drawing operation, and drawn into a sheath blank of the required size ; After leaving the heating furnace, use water cooling to cool the steel bars to 920-950 °C at a cooling rate of 23-25 °C / s, and then cool them to r...
Embodiment 2
[0040] This embodiment provides a processing technology for a wear-resistant and impact-resistant pile foundation steel casing. The chemical composition of the selected steel blank is: C: 0.38%, Si: 0.30%, Mn: 1.0%, Cr: 1.0% , Mo: 0.22%, N: 0.030%, P: 0.032%, S: 0.0018%, Nb: 0.25%, V: 0.36%, rare earth: 0.25%, 0.8% residual elements, the rest is Fe;
[0041] Among the rare earths, the following components are contained by weight percentage: Gd: 18%, Pr: 5%, Dy: 9%, Ac: 12.8%, Nd: 20%, Sm: 13%, and the balance is La;
[0042] Specifically include the following steps:
[0043] Step (1): Put the above-mentioned steel blank in a furnace and heat it to 1300-1400°C. After the steel blank is heated, it is drawn into a closed environment of methane or ethane for drawing operation, and drawn into a sheath blank of the required size ; After exiting the heating furnace, use water cooling to cool the steel bar to 920-950 ° C at a cooling rate of 23-25 ° C / s, and then cool it to room te...
Embodiment 3
[0049] This embodiment provides a processing technology for a wear-resistant and impact-resistant pile foundation steel casing. The chemical composition of the selected steel blank is: C: 0.3%, Si: 0.25%, Mn: 0.9%, Cr: 0.9% , Mo: 0.20%, N: 0.20%, P: 0.25%, S: 0.0015%, Nb: 0.02%, V: 0.25%, rare earth: 0.24%, 0.6% residual elements, the rest is Fe;
[0050] Among the rare earths, the following components are contained by weight percentage: Gd: 16%, Pr: 4%, Dy: 8%, Ac: 12.6%, Nd: 18%, Sm: 12%, and the balance is La;
[0051] Specifically include the following steps:
[0052] Step (1): Put the above-mentioned steel blank in a furnace and heat it to 1300-1400°C. After the steel blank is heated, it is drawn into a closed environment of methane or ethane for drawing operation, and drawn into a sheath blank of the required size ; After exiting the heating furnace, use water cooling to cool the steel bar to 920-950 ° C at a cooling rate of 23-25 ° C / s, and then cool it to room tem...
PUM
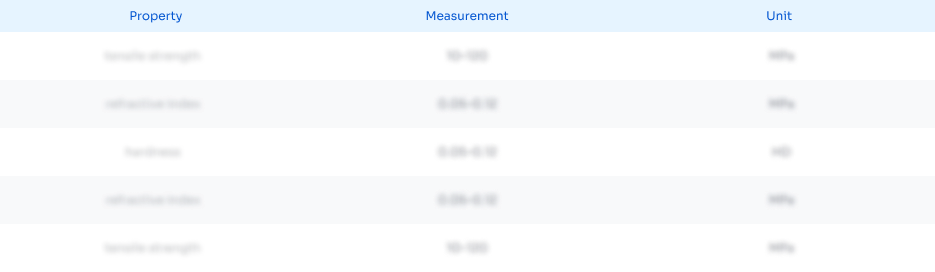
Abstract
Description
Claims
Application Information

- R&D
- Intellectual Property
- Life Sciences
- Materials
- Tech Scout
- Unparalleled Data Quality
- Higher Quality Content
- 60% Fewer Hallucinations
Browse by: Latest US Patents, China's latest patents, Technical Efficacy Thesaurus, Application Domain, Technology Topic, Popular Technical Reports.
© 2025 PatSnap. All rights reserved.Legal|Privacy policy|Modern Slavery Act Transparency Statement|Sitemap|About US| Contact US: help@patsnap.com