Preparation method of tetrabutylthiuram disulfide used as rubber vulcanization accelerator
A technology of tetrabenzylthiuram disulfide and rubber vulcanization, which is applied in the chemical industry, can solve the problems of no recovery of carbon disulfide, safety problems, and unstable safety, and achieve short vulcanization time, less pollution, and long burning time Effect
- Summary
- Abstract
- Description
- Claims
- Application Information
AI Technical Summary
Problems solved by technology
Method used
Image
Examples
Embodiment 1
[0042] A preparation method of rubber vulcanization accelerator tetrabenzylthiuram disulfide, the steps are as follows:
[0043] (1) Under normal pressure, add dibenzylamine and sodium hydroxide into water, stir and mix evenly, add carbon disulfide dropwise at 23°C, and stir for 0.5h;
[0044] The molar ratio of dibenzylamine, sodium hydroxide and carbon disulfide is 1:1.1:1.35, and the molar volume ratio of dibenzylamine to water is 1:2mol / L;
[0045] (2) The reaction solution obtained in step (1) was left to stand for 0.5h, unreacted carbon disulfide was separated from the bottom, and 10wt% hydrogen peroxide was added dropwise at 58.5°C for oxidation reaction, and the amount added was the total amount of hydrogen peroxide 70% of the total amount of hydrogen peroxide, reacted for 3h, then added dropwise 20wt% hydrogen peroxide, the amount added was 30% of the total amount of hydrogen peroxide, continued the oxidation reaction for 1h, and controlled the rate of addition to 0.8ml...
Embodiment 2
[0068] A kind of preparation method of rubber vulcanization accelerator tetrabenzylthiuram disulfide, step is the same as embodiment 1, and difference is:
[0069] The molar ratio of dibenzylamine, sodium hydroxide and carbon disulfide is 1:1.12:1.15, and other conditions are the same as in Example 1.
[0070] The color of the obtained product is white. After testing, the initial melting point of the product is 132.3° C., the purity of the product is 98.1%, and the yield of the reaction is 95.5%.
Embodiment 3
[0072] A kind of preparation method of rubber vulcanization accelerator tetrabenzylthiuram disulfide, step is the same as embodiment 1, and difference is:
[0073] The molar ratio of hydrogen peroxide to dibenzylamine is 0.8:1, and other conditions are the same as in Example 1.
[0074] The color of the obtained product is white. After testing, the initial melting point of the product is 132.6° C., the purity of the product is 97.9%, and the yield of the reaction is 95.8%.
PUM
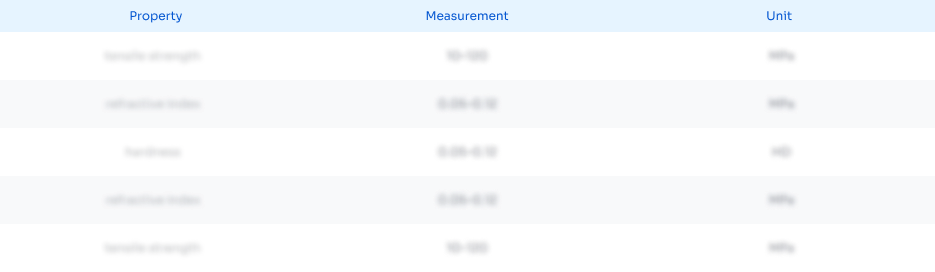
Abstract
Description
Claims
Application Information

- Generate Ideas
- Intellectual Property
- Life Sciences
- Materials
- Tech Scout
- Unparalleled Data Quality
- Higher Quality Content
- 60% Fewer Hallucinations
Browse by: Latest US Patents, China's latest patents, Technical Efficacy Thesaurus, Application Domain, Technology Topic, Popular Technical Reports.
© 2025 PatSnap. All rights reserved.Legal|Privacy policy|Modern Slavery Act Transparency Statement|Sitemap|About US| Contact US: help@patsnap.com