Fully synthesized magnesium alloy cutting fluid and preparation method thereof
A technology of cutting fluid and magnesium alloy, applied in lubricating compositions, petroleum industry, etc., can solve problems such as difficult cleaning, and achieve the effects of easy cleaning, good chip sinking, good cooling and cleaning properties
- Summary
- Abstract
- Description
- Claims
- Application Information
AI Technical Summary
Problems solved by technology
Method used
Examples
Embodiment 1
[0026] In the fully synthetic magnesium alloy cutting fluid of this embodiment, the cutting fluid raw materials include the following components by weight: Sorbitan monooleate: 15-17 parts, polyethylene glycol oleate: 5-7 parts, diethylene glycol Amine: 5-7 parts, Dipotassium EDTA: 5-7 parts, Fatty alcohol polyoxyethylene ether sodium sulfate: 5-7 parts, Sodium oleate: 6-8 parts, Potassium naphthenate: 7- 9 parts, lauryl dimethyl benzyl ammonium chloride: 5-7 parts, triethanolamine oleate: 3-5 parts, caprylic acid: 5-8 parts, coconut oil fatty acid diethanolamide: 3-4 parts Parts, diethyltriaminepentaacetic acid: 3-5 parts, butyl carbitol: 6-8 parts, diisopropanolamine: 3-4 parts, octylphenol polyoxyethylene ether: 5-7 parts, Ricinoleic acid: 4-7 parts, fatty acid sorbitan: 0.5-1 part, Bioxad BIT-10: 2-5 parts, additives: 10-15 parts, deionized water: 35-40 parts.
[0027] In this example, the preparation method of sodium oleate is as follows: first heat up the industrial ole...
Embodiment 2
[0034] In the fully synthetic magnesium alloy cutting fluid of this embodiment, the cutting fluid raw materials include the following components in parts by weight: Sorbitan monooleate: 15 parts, polyethylene glycol oleate: 5 parts, diglycolamine: 5 parts , Dipotassium EDTA: 5 parts, Sodium fatty alcohol polyoxyethylene ether sulfate: 5 parts, Sodium oleate: 6 parts, Potassium naphthenate: 7 parts, Dodecyl dimethyl benzyl chloride Ammonium: 5 parts, triethanolamine oleate: 3 parts, caprylic acid: 5 parts, coconut oil fatty acid diethanolamide: 3 parts, diethyltriaminepentaacetic acid: 3 parts, butyl carbitol: 6 parts, Diisopropanolamine: 3 parts, octylphenol polyoxyethylene ether: 5 parts, ricinoleic acid: 4 parts, fatty acid sorbitan: 0.5 parts, Bioxad BIT-10: 2 parts, additives: 10 parts, Ionized water: 35 parts.
[0035] In this example, the preparation method of sodium oleate is as follows: first heat up the industrial oleic acid to 70°C, then slowly add 50% aqueous sodiu...
Embodiment 3
[0044] In the fully synthetic magnesium alloy cutting fluid of this embodiment, the cutting fluid raw materials include the following components in parts by weight: sorbitan monooleate: 17 parts, polyethylene glycol oleate: 7 parts, diglycolamine: 7 parts , Dipotassium EDTA: 7 parts, Sodium fatty alcohol polyoxyethylene ether sulfate: 7 parts, Sodium oleate: 8 parts, Potassium naphthenate: 9 parts, Dodecyl dimethyl benzyl chloride Ammonium: 7 parts, triethanolamine oleate: 5 parts, caprylic acid: 8 parts, coconut oil fatty acid diethanolamide: 4 parts, diethyltriaminepentaacetic acid: 5 parts, butyl carbitol: 8 parts, Diisopropanolamine: 4 parts, octylphenol polyoxyethylene ether: 7 parts, ricinoleic acid: 7 parts, fatty acid sorbitan: 1 part, Bioxad BIT-10: 5 parts, additives: 15 parts, Ionized water: 40 parts.
[0045] In this example, the preparation method of sodium oleate is as follows: first heat up the industrial oleic acid to 70°C, then slowly add 50% aqueous sodium h...
PUM
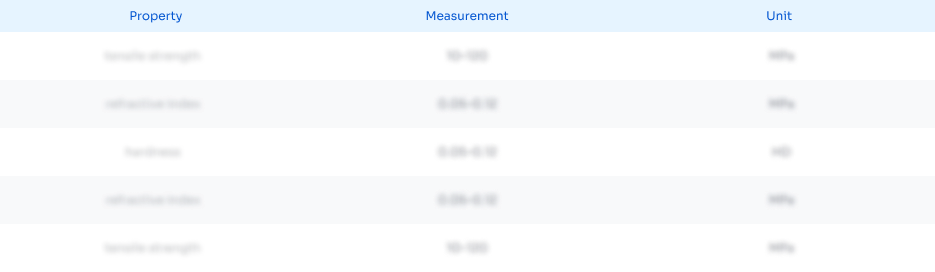
Abstract
Description
Claims
Application Information

- Generate Ideas
- Intellectual Property
- Life Sciences
- Materials
- Tech Scout
- Unparalleled Data Quality
- Higher Quality Content
- 60% Fewer Hallucinations
Browse by: Latest US Patents, China's latest patents, Technical Efficacy Thesaurus, Application Domain, Technology Topic, Popular Technical Reports.
© 2025 PatSnap. All rights reserved.Legal|Privacy policy|Modern Slavery Act Transparency Statement|Sitemap|About US| Contact US: help@patsnap.com