Preparation method for paraffin microcapsule phase-change material modified by graphene oxide
A paraffin microcapsule, graphene modification technology, applied in the directions of microcapsule preparation, microsphere preparation, chemical instruments and methods, etc., to achieve the effects of prolonging service life, improving thermal stability, and good practical economic value
- Summary
- Abstract
- Description
- Claims
- Application Information
AI Technical Summary
Problems solved by technology
Method used
Image
Examples
Embodiment 1
[0024] On a magnetic stirrer, in a low temperature (0-4°C) ice-water bath, add 1g of 38 mesh graphite, 98% concentrated sulfuric acid, sodium nitrate, and potassium permanganate, of which graphite: concentrated sulfuric acid: sodium nitrate: potassium permanganate = 1:50:0.6:6, preliminary oxidation of graphite; water bath at medium temperature (35-40°C), slowly add potassium permanganate one by one, among which graphite: potassium permanganate=1:6, keep stirring; high temperature (80- 90℃) water bath to complete the deep oxidation of graphite, wherein graphite: potassium permanganate = 1:3; add deionized water, graphite: deionized water = 1:60, after the hydrolysis reaction, add 30Vol% hydrogen peroxide and unreacted potassium permanganate, add 10Vol% hydrochloric acid solution after the solution is bright yellow, wherein 30Vol% hydrogen peroxide: 10Vol% hydrochloric acid=1:1.5, vacuum filter, wash with deionized water to pH value 7, and obtained graphene oxide by drying and ...
Embodiment 2
[0026] On a magnetic stirrer, in a low temperature (0-4°C) ice-water bath, add 1g of 50 mesh graphite, 98% concentrated sulfuric acid, sodium nitrate, and potassium permanganate, of which graphite: concentrated sulfuric acid: sodium nitrate: potassium permanganate = 1:60:1:3, preliminary oxidation of graphite; water bath at medium temperature (35-40°C), slowly add potassium permanganate one by one, among which graphite: potassium permanganate=1:3, keep stirring; high temperature (80- 90℃) water bath to complete the deep oxidation of graphite, wherein graphite: potassium permanganate = 1:3; add deionized water, graphite: deionized water = 1:70, after the hydrolysis reaction, add 30Vol% hydrogen peroxide And unreacted potassium permanganate, after the solution is bright yellow, add 10Vol% hydrochloric acid solution, wherein 30Vol% hydrogen peroxide: 10Vol% hydrochloric acid=1:2, vacuum filter, wash with deionized water to pH value 7, and obtained graphene oxide by drying and gri...
Embodiment 3
[0028] On a magnetic stirrer, in a low-temperature (0-4°C) ice-water bath, add 1g of 200 mesh graphite, 98% concentrated sulfuric acid, sodium nitrate, and potassium permanganate, of which graphite: concentrated sulfuric acid: sodium nitrate: potassium permanganate = 1:70:0.5:3, preliminary oxidation of graphite; water bath at medium temperature (35-40°C), slowly add potassium permanganate one by one, among which graphite: potassium permanganate=1:3, keep stirring; high temperature (80- 90°C) water bath to complete the deep oxidation of graphite, where graphite: potassium permanganate = 1:3; add deionized water, graphite: deionized water = 1:80, after the hydrolysis reaction, add 30Vol% hydrogen peroxide And unreacted potassium permanganate, after the solution is bright yellow, add 10Vol% hydrochloric acid solution, wherein 30Vol% hydrogen peroxide: 10Vol% hydrochloric acid=1:2, vacuum filter, wash with deionized water to pH value 7, and obtained graphene oxide by drying and g...
PUM
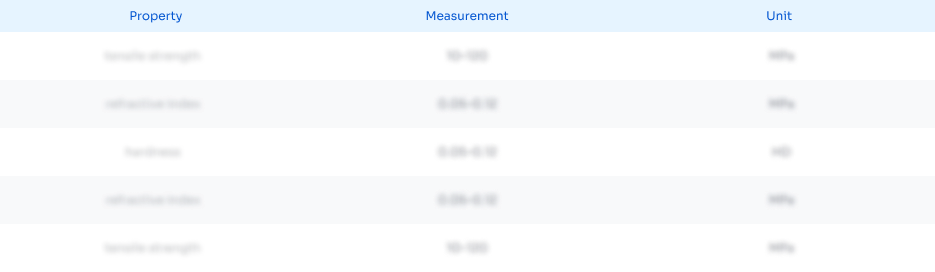
Abstract
Description
Claims
Application Information

- R&D
- Intellectual Property
- Life Sciences
- Materials
- Tech Scout
- Unparalleled Data Quality
- Higher Quality Content
- 60% Fewer Hallucinations
Browse by: Latest US Patents, China's latest patents, Technical Efficacy Thesaurus, Application Domain, Technology Topic, Popular Technical Reports.
© 2025 PatSnap. All rights reserved.Legal|Privacy policy|Modern Slavery Act Transparency Statement|Sitemap|About US| Contact US: help@patsnap.com