Drive gear and preparation method thereof
A driving gear and tooth profile technology, which is applied in the field of driving gear and its preparation, can solve the problems of short life, low gear hardness and impact toughness, etc., to improve strength, increase hardenability, increase corrosion resistance and oxidation resistance. Effect
- Summary
- Abstract
- Description
- Claims
- Application Information
AI Technical Summary
Problems solved by technology
Method used
Examples
Embodiment 1
[0035] A driving gear provided in this embodiment, the chemical composition of the driving gear is: C: 0.20%, Si: 0.35%, Mn: 0.50%, Cr: 1.6%, Ni: 3.4%, Nb: 0.04%, V: 0.03%, Cu: 0.4%, P: 0.03%, S: 0.025%, lanthanide rare earth: 0.03%, the balance is Fe;
[0036] The chemical composition of the lanthanide rare earth components by weight percentage is: La: 20%, Sc: 12%, Y: 16%, Sm: 21%; Gd: 20%, and other lanthanide elements: 11%.
[0037] The preparation method of above-mentioned drive gear, specifically carries out according to the following steps:
[0038] (1) The driving gear mold is made of molding sand and core sand as molding materials. Before making the mold, the molding sand in the molding material is first placed in an oven for drying;
[0039] (2) Heat and melt the chemical composition of the driving gear at 1650°C, inject it into the mold formed in step (1), and release it after air cooling to obtain the driving gear blank;
[0040] (3) For the drive gear blank in ste...
Embodiment 2
[0048] A drive gear provided in this embodiment, the chemical composition of the drive gear is: C: 0.23%, Si: 0.33%, Mn: 0.55%, Cr: 1.5%, Ni: 3.2%, Nb: 0.03%, V: 0.01%, Cu: 0.2%, P: 0.025%, S: 0.018%, lanthanide rare earth: 0.01%, the balance is Fe;
[0049] The chemical composition of the lanthanide rare earth components by weight percentage is: La: 23%, Sc: 11%, Y: 15%, Sm: 20%; Gd: 19%, and other lanthanide elements: 12%.
[0050] The preparation method of above-mentioned drive gear, specifically carries out according to the following steps:
[0051] (1) The driving gear mold is made of molding sand and core sand as molding materials. Before making the mold, the molding sand in the molding material is first placed in an oven for drying;
[0052] (2) Heat and melt the chemical composition of the driving gear at 1660°C, inject it into the mold formed in step (1), and release it after air cooling to obtain the driving gear blank;
[0053] (3) For the drive gear blank in step...
Embodiment 3
[0061] A drive gear provided in this embodiment, the chemical composition of the drive gear is: C: 0.22%, Si: 0.30%, Mn: 0.60%, Cr: 1.4%, Ni: 3.3%, Nb: 0.02%, V: 0.02%, Cu: 0.3%, P: 0.01%, S: 0.029%, lanthanide rare earth: 0.02%, the balance is Fe;
[0062] The chemical composition of the lanthanide rare earth is: La: 22%, Sc: 11%, Y: 17%, Sm: 21%; Gd: 19%, and other lanthanide elements: 10%.
[0063] The preparation method of above-mentioned drive gear, specifically carries out according to the following steps:
[0064] (1) The driving gear mold is made of molding sand and core sand as molding materials. Before making the mold, the molding sand in the molding material is first placed in an oven for drying;
[0065] (2) Heat and melt the chemical composition of the driving gear at 1670°C, inject it into the mold formed in step (1), and release it after air cooling to obtain the driving gear blank;
[0066] (3) For the driving gear blank in step (2), heat it at 305°C, then co...
PUM
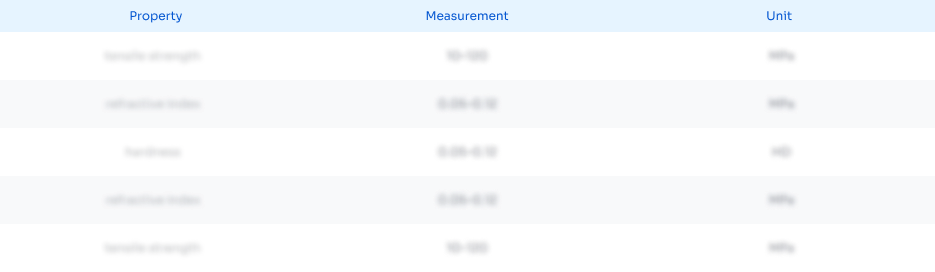
Abstract
Description
Claims
Application Information

- R&D Engineer
- R&D Manager
- IP Professional
- Industry Leading Data Capabilities
- Powerful AI technology
- Patent DNA Extraction
Browse by: Latest US Patents, China's latest patents, Technical Efficacy Thesaurus, Application Domain, Technology Topic, Popular Technical Reports.
© 2024 PatSnap. All rights reserved.Legal|Privacy policy|Modern Slavery Act Transparency Statement|Sitemap|About US| Contact US: help@patsnap.com