High-efficient process for manufacturing polycrystalline silicon cast ingots
A production process and polysilicon technology, applied in the field of photovoltaics, can solve problems such as affecting the photoelectric conversion efficiency of solar cells, fast phosphorus diffusion, and troublesome processing technology, and achieve the effects of low cost, high efficiency cost, and fewer crystal defects.
- Summary
- Abstract
- Description
- Claims
- Application Information
AI Technical Summary
Problems solved by technology
Method used
Examples
Embodiment 1
[0043] Embodiment 1: A kind of manufacturing process of high-efficiency polysilicon ingot, comprises the following steps:
[0044] (1) Raw materials: 60% of primary polysilicon, 40% of polycrystalline auxiliary materials; polycrystalline auxiliary materials are one or more of crushed polycrystalline, polycrystalline scrap, polycrystalline tailings, and single crystal tailings;
[0045] (2) Cleaning of raw materials: Clean the polycrystalline skin, polycrystalline tailings and single crystal tailings with a mixed solution of nitric acid and hydrofluoric acid, the volume ratio of nitric acid and hydrofluoric acid is 11.8:2, and the cleaning time is 2 minutes , and finally rinse with pure water; the broken silicon wafers are cleaned with a mixed solution of nitric acid and hydrofluoric acid, the volume ratio of nitric acid and hydrofluoric acid is 11.8:1, and the cleaning time is 1 minute, and finally cleaned with pure water under ultrasonic conditions. Rinse, ultrasonic power is...
Embodiment 2
[0078] Embodiment 2: A kind of manufacturing process of high-efficiency polysilicon ingot, comprises the following steps:
[0079] (1) Raw materials: primary polysilicon 65%, polycrystalline auxiliary materials 35%; polycrystalline auxiliary materials are one or more of crushed polycrystalline, polycrystalline scraps, polycrystalline tailings, and single crystal tailings;
[0080] (2) Cleaning of raw materials: Clean the polycrystalline skin, polycrystalline tailings and single crystal tailings with a mixed solution of nitric acid and hydrofluoric acid, the volume ratio of nitric acid and hydrofluoric acid is 12:2, and the cleaning time is 2.5 minutes , and finally rinse with pure water; the broken silicon wafers are cleaned with a mixed solution of nitric acid and hydrofluoric acid, the volume ratio of nitric acid and hydrofluoric acid is 12:1, the cleaning time is 2 minutes, and finally cleaned with pure water under ultrasonic conditions Rinse, ultrasonic power is 2.9KW; The...
Embodiment 3
[0113] Embodiment three: a kind of high-efficiency polysilicon ingot manufacturing process comprises the following steps:
[0114] (1) Raw materials: 70% of primary polysilicon, 30% of polycrystalline auxiliary materials; polycrystalline auxiliary materials are one or more of crushed polycrystalline, polycrystalline scraps, polycrystalline tailings, and single crystal tailings;
[0115] (2) Cleaning of raw materials: Clean the polycrystalline skin, polycrystalline tailings and single crystal tailings with a mixed solution of nitric acid and hydrofluoric acid, the volume ratio of nitric acid and hydrofluoric acid is 12.2:2, and the cleaning time is 3 minutes , and finally rinse with pure water; the broken silicon chips are cleaned with a mixed solution of nitric acid and hydrofluoric acid, the volume ratio of nitric acid and hydrofluoric acid is 12.2:1, the cleaning time is 3 minutes, and finally cleaned with pure water under ultrasonic conditions Rinse, ultrasonic power is 3KW...
PUM
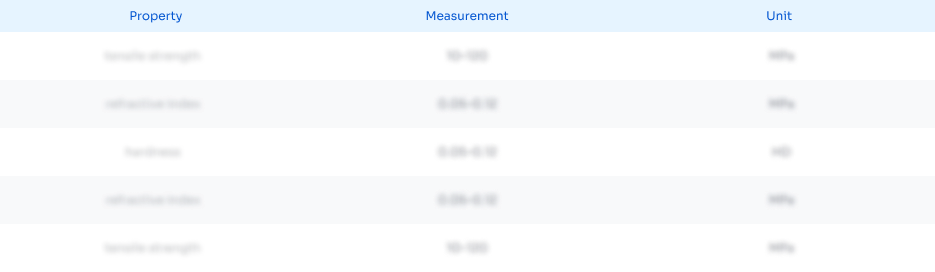
Abstract
Description
Claims
Application Information

- R&D
- Intellectual Property
- Life Sciences
- Materials
- Tech Scout
- Unparalleled Data Quality
- Higher Quality Content
- 60% Fewer Hallucinations
Browse by: Latest US Patents, China's latest patents, Technical Efficacy Thesaurus, Application Domain, Technology Topic, Popular Technical Reports.
© 2025 PatSnap. All rights reserved.Legal|Privacy policy|Modern Slavery Act Transparency Statement|Sitemap|About US| Contact US: help@patsnap.com