Iron-containing zinc powder recycling process
A technology of dust recovery and process, which is applied in the field of recycling and utilization of iron and zinc dust produced in iron and steel process, and can solve problems such as blockage of smoke exhaust channels, high coke ratio, high S and P content in molten iron, etc.
- Summary
- Abstract
- Description
- Claims
- Application Information
AI Technical Summary
Problems solved by technology
Method used
Examples
Embodiment 1
[0029] 1) Recycling and drying iron and zinc-containing dust in iron and steel plant;
[0030] 2) Mix the dried dust with coal powder and binder in proportion, the ratio of dust to coal powder is C / O=1.1, and the ratio of binder is 2%;
[0031] 3) Pellet the mixed dust on a pelletizing machine to obtain raw pellets, the diameter of which is about 25mm, plus or minus 5mm;
[0032] 4) The raw pellets are fed into the shaft furnace, and are gradually heated to 1200°C by the gas rising from the bottom from top to bottom, and a self-reduction reaction occurs. 3 above;
[0033] 5) Zinc is reduced in the lower part of the blast furnace to form zinc vapor, which together with the rising gas is discharged from the shaft furnace at 300°C and enters the two-stage dust collector;
[0034] 6) The gas carrying zinc vapor enters the heat exchanger after the initial dedusting, and the heat generated by the heat exchange is used to dry the zinc-rich dust; the dedusting ash has low zinc conte...
Embodiment 2
[0038] 1) Recycling and drying iron and zinc-containing dust in iron and steel plant;
[0039] 2) Mix the dried dust with coal powder and binder in proportion, the ratio of dust to coal powder is C / O=1.5, and the binder ratio is 10%;
[0040] 3) Pellet the mixed dust on a pelletizing machine to obtain raw pellets, the diameter of which is about 25mm, plus or minus 5mm;
[0041] 4) The green pellets are fed into the shaft furnace, and are gradually heated to 1250°C by the gas rising from the bottom from top to bottom, and a self-reduction reaction occurs. 3 above;
[0042] 5) Zinc is reduced in the lower part of the blast furnace to form zinc vapor, which together with the rising gas is discharged from the shaft furnace at 700°C and enters the two-stage dust collector;
[0043] 6) The gas carrying zinc vapor enters the heat exchanger after the initial dedusting, and the heat generated by the heat exchange is used to dry the zinc-rich dust; the dedusting ash has low zinc conte...
Embodiment 3
[0047] 1) Recycling and drying iron and zinc-containing dust in iron and steel plant;
[0048] 2) Mix the dried dust, coal powder and binder in proportion, the ratio of dust to coal powder is 1.2, and the binder ratio is 4%;
[0049] 3) Pellet the mixed dust on a pelletizing machine to obtain raw pellets, the diameter of which is about 25mm, plus or minus 5mm;
[0050] 4) The raw pellets are fed into the shaft furnace, and are gradually heated to 1225°C by the gas rising from the bottom from top to bottom, and a self-reduction reaction occurs. 3 above;
[0051] 5) Zinc is reduced in the lower part of the blast furnace to form zinc vapor, which together with the rising gas is discharged from the shaft furnace at 500°C and enters the two-stage dust collector;
[0052] 6) The gas carrying zinc vapor enters the heat exchanger after the initial dedusting, and the heat generated by the heat exchange is used to dry the zinc-rich dust; the dedusting ash has low zinc content and can ...
PUM
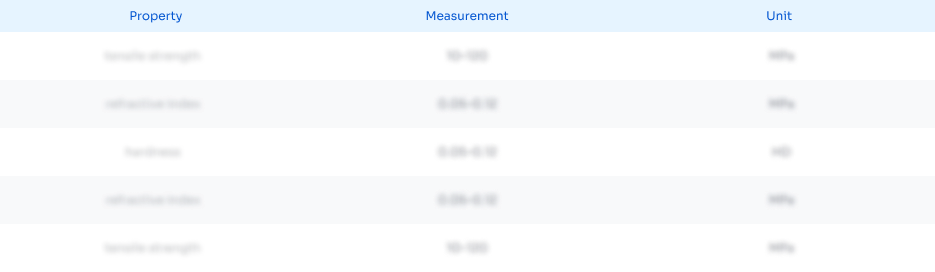
Abstract
Description
Claims
Application Information

- R&D
- Intellectual Property
- Life Sciences
- Materials
- Tech Scout
- Unparalleled Data Quality
- Higher Quality Content
- 60% Fewer Hallucinations
Browse by: Latest US Patents, China's latest patents, Technical Efficacy Thesaurus, Application Domain, Technology Topic, Popular Technical Reports.
© 2025 PatSnap. All rights reserved.Legal|Privacy policy|Modern Slavery Act Transparency Statement|Sitemap|About US| Contact US: help@patsnap.com