Method for preparing olefins by using dehydrogenation of light alkanes with sulfur-containing substances added in raw materials
A dehydrogenation and material technology, applied in chemical instruments and methods, metal/metal oxide/metal hydroxide catalysts, hydrocarbons, etc., can solve problems such as the inability to control the vulcanization depth as required
- Summary
- Abstract
- Description
- Claims
- Application Information
AI Technical Summary
Problems solved by technology
Method used
Examples
preparation example Construction
[0012] The dehydrogenation catalyst can be prepared by a conventional method, such as using an impregnation method to support the dehydrogenation active metal, and the auxiliary agent can be introduced during the preparation of the alumina or weakly acidic molecular sieve carrier and / or by an impregnation method.
[0013] The catalyst of the present invention uses alumina or weakly acidic molecular sieve as a carrier, and the dehydrogenation active metal component is generally selected from one or more of platinum, palladium, iridium, rhodium or osmium in the platinum group, and the amount used is calculated as a carrier 0.01%~2% of the weight. The content of Sn is 0.1%~10% of the weight of the carrier in terms of simple substance.
[0014] In the dehydrogenation catalyst based on alumina or weakly acidic molecular sieve of the present invention, the dehydrogenation active metal component can be evenly distributed in the catalyst, preferably the dehydrogenation active metal co...
example 1
[0029] The spinel phase carrier was impregnated with tin tetrachloride ethanol solution, dried, and calcined at 600°C for 4 hours to obtain a spinel phase containing 0.3wt% Sn. The spinel phase containing 0.3wt% Sn was calcined at 800°C for 3h, the calcined support was impregnated with an aqueous solution containing chloroplatinic acid for 6h at 70°C, dried at 120°C for 2h, and calcined at 500°C for 4h. Dechlorination in air containing 20v% water vapor at 450°C for 4h. Then at 70 °C with KNO 3 Soaked in aqueous solution for 2h, dried and roasted under the same conditions. The loading amount of each component in the catalyst is: Pt 0.5wt%, Sn 0.3wt%, K0.5wt%.
[0030] evaluation conditions : volumetric space velocity 2000 h -1 , the reaction temperature is 600°C, the raw material for dehydrogenation is a mixed raw material with a molar ratio of hydrogen:isobutane of 2:1, and the content of methyl mercaptan in the raw material for dehydrogenation is 10 μmol / mol.
[0031] ...
example 2
[0038] The dehydrogenation catalyst was prepared in the same manner as in Example 1.
[0039] evaluation conditions : volumetric space velocity 2000 h -1 , the reaction temperature is 600°C, the raw material for dehydrogenation is a mixture with a molar ratio of hydrogen: isobutane of 2:1, and the content of methyl mercaptan in the raw material for dehydrogenation is 5 μmol / mol.
[0040] Evaluation results : After continuous evaluation of the catalyst for 40 hours, the conversion rate of isobutane was 46.8%, the selectivity of isobutene was 98.1%, the conversion rate decreased by 2.8 percentage points, the selectivity remained basically unchanged, and the carbon deposition amount was only 0.39%, showing good catalytic performance. activity and stability.
PUM
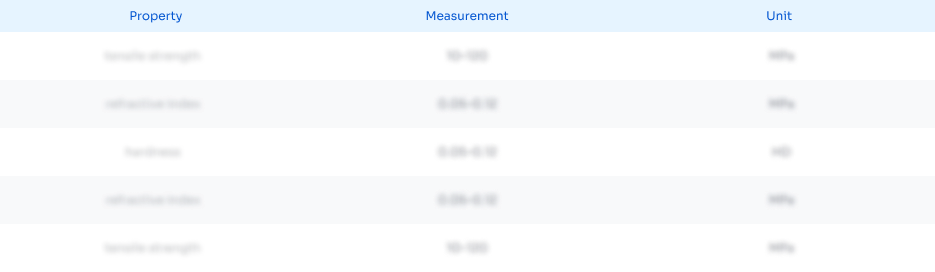
Abstract
Description
Claims
Application Information

- R&D
- Intellectual Property
- Life Sciences
- Materials
- Tech Scout
- Unparalleled Data Quality
- Higher Quality Content
- 60% Fewer Hallucinations
Browse by: Latest US Patents, China's latest patents, Technical Efficacy Thesaurus, Application Domain, Technology Topic, Popular Technical Reports.
© 2025 PatSnap. All rights reserved.Legal|Privacy policy|Modern Slavery Act Transparency Statement|Sitemap|About US| Contact US: help@patsnap.com