Device and method for compensating composition error of main shaft in real time
A comprehensive error, real-time compensation technology, applied in other manufacturing equipment/tools, metal processing mechanical parts, maintenance and safety accessories, etc., can solve the problems of precision machining errors, slow response speed, complex methods, etc., to achieve rapid measurement and compensation , Improve the effect of error compensation accuracy
- Summary
- Abstract
- Description
- Claims
- Application Information
AI Technical Summary
Problems solved by technology
Method used
Image
Examples
Embodiment 1
[0050] refer to Figure 1~Figure 3 , a spindle comprehensive error real-time compensation device, comprising a radial capacitive displacement sensor 1, an axial capacitive displacement sensor 2, a control computer 3, a two-degree-of-freedom fast-tool servo controller 4 and a two-degree-of-freedom fast-tool servo unit 5, the radial capacitive displacement The output end of the sensor 1 is connected with the first input end of the control computer 3, the output end of the axial capacitive displacement sensor 2 is connected with the second input end of the control computer 3, and the two-degree-of-freedom fast knife servo controller 4 is respectively connected with the control computer 3 and the control computer 3. Two-degree-of-freedom fast-knife servo unit 5 connections;
[0051] The two-degree-of-freedom fast tool servo unit 5 is connected to the processing tool 0, the radial capacitive displacement sensor 1 is installed on one side of the processing tool 0 and its axis is per...
Embodiment 2
[0060] A real-time compensation method for a comprehensive error of a spindle, comprising:
[0061] S1. Use the radial capacitive displacement sensor to collect the real-time radial displacement of the workpiece and send it to the control computer, and at the same time use the axial capacitive displacement sensor to collect the real-time axial displacement of the workpiece and send it to the control computer;
[0062] S2. The control computer receives the real-time radial displacement and axial displacement of the workpiece and compares them with the preset radial displacement and preset axial displacement respectively, and then calculates the radial error and axial error of the workpiece and sends them to Two-degree-of-freedom fast-tool servo controller; the preset radial displacement and preset axial displacement are set processing parameters for the workpiece. For example, if there is a difference between the real-time radial displacement and the preset radial displacement, ...
PUM
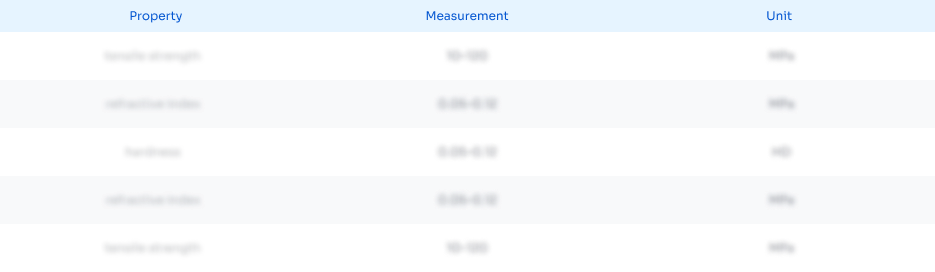
Abstract
Description
Claims
Application Information

- Generate Ideas
- Intellectual Property
- Life Sciences
- Materials
- Tech Scout
- Unparalleled Data Quality
- Higher Quality Content
- 60% Fewer Hallucinations
Browse by: Latest US Patents, China's latest patents, Technical Efficacy Thesaurus, Application Domain, Technology Topic, Popular Technical Reports.
© 2025 PatSnap. All rights reserved.Legal|Privacy policy|Modern Slavery Act Transparency Statement|Sitemap|About US| Contact US: help@patsnap.com