Ceramic composite material substrate and manufacturing technology thereof
A technology for preparing composite materials and substrates, which is applied in the field of metal-containing ceramic substrates and its preparation technology, can solve the problems of electronic chip mismatch and low thermal conductivity, and achieve improved chip heat dissipation, easy impregnation of metals, and convenient and efficient preparation Effect
- Summary
- Abstract
- Description
- Claims
- Application Information
AI Technical Summary
Problems solved by technology
Method used
Image
Examples
Embodiment 1
[0029] see figure 1 flow chart. Take 650 g of SiC powder with an average particle size of 3 μm, add 150 g of water, 150 g of styrene-acrylic emulsion binder, 40 g of glycerin plasticizer, and 10 g of triolein dispersant, and perform ball milling and mixing for 12 hours to prepare a cast slurry. The obtained slurry is cast on a tape casting machine, and the slurry passes through the casting freeze-drying zone, directional condensed, and forms vertically penetrating and uniformly distributed columnar icicles in the semi-finished raw tape, and then condenses to form uniformly distributed columnar icicles The semi-finished raw tape was freeze-dried at -20°C for 4 hours to form a porous ceramic green tape with evenly distributed open pores and perpendicular to the surface of the ceramic green tape. The ceramic raw tape is heated to remove the glue, and the temperature is raised to 500° C., and kept for 3 hours. After the glue is removed, a porous ceramic green sheet with open po...
Embodiment 2
[0031] Take 680g of AlN powder with an average particle size of 1 μm, add 140g of water, 130g of styrene-acrylic emulsion binder, 40g of glycerin plasticizer, and 10g of triolein dispersant, and carry out ball milling and mixing for 12 hours to prepare the casting slurry. The obtained slurry is cast on a tape casting machine, and the slurry passes through the casting freeze-drying zone, directional condensed, and forms vertically penetrating and uniformly distributed columnar icicles in the semi-finished raw tape, and then condenses to form uniformly distributed columnar ice The semi-finished green tape of the column is freeze-dried at -30°C for 3 hours to form a porous ceramic green tape with evenly distributed open pores and perpendicular to the surface of the ceramic green tape. The ceramic raw tape is heated to remove the glue, and the temperature is raised to 700° C., and kept for 1 hour. After the glue is removed, a porous ceramic green sheet with open pores evenly distr...
Embodiment 3
[0033] Take Al with an average particle size of 1 μm 2 o 3 Powder 500g and low melting point glass additive powder 200g, add water 150g, styrene-acrylic emulsion binder 150g, glycerin plasticizer 40g, triolein dispersant 10g, carry out ball milling and mix for 12 hours, prepare the fluid Extension slurry. The obtained slurry is cast on a tape casting machine, the slurry passes through the casting freeze-drying zone, the slurry passes through the casting freeze-drying zone, directional condensation forms vertically penetrating and evenly distributed columnar icicles in the raw tape semi-finished product, Then, freeze-dry the green tape semi-finished product that condenses to form evenly distributed columnar icicles at a temperature of -40°C for 2 hours to form a porous ceramic green tape with evenly distributed open pores and perpendicular to the surface of the ceramic green tape. The ceramic raw tape is heated to remove the glue, and the temperature is raised to 600° C., and...
PUM
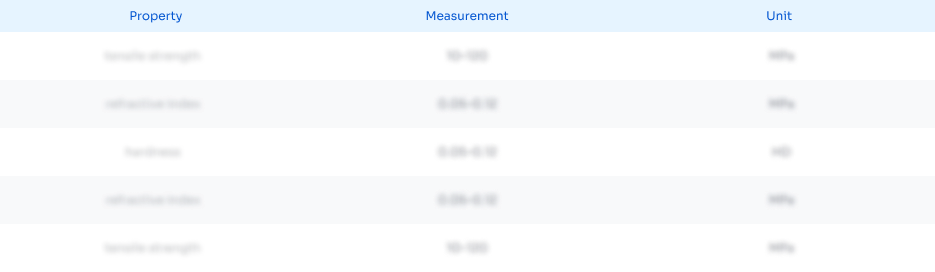
Abstract
Description
Claims
Application Information

- Generate Ideas
- Intellectual Property
- Life Sciences
- Materials
- Tech Scout
- Unparalleled Data Quality
- Higher Quality Content
- 60% Fewer Hallucinations
Browse by: Latest US Patents, China's latest patents, Technical Efficacy Thesaurus, Application Domain, Technology Topic, Popular Technical Reports.
© 2025 PatSnap. All rights reserved.Legal|Privacy policy|Modern Slavery Act Transparency Statement|Sitemap|About US| Contact US: help@patsnap.com