A modification method for surface etching and bonding of β-cyclodextrin to membrane artificial lung by using low-temperature plasma
A technology of low-temperature plasma and surface etching, applied in chemical instruments and methods, membrane technology, semi-permeable membrane separation, etc., can solve problems such as uncontrollable influence of surface functionalization, random degradation and etching, etc., and achieve good biophase Effects of capacitive and anti-pollution performance, reduction of pure water contact angle, and improvement of biocompatibility
- Summary
- Abstract
- Description
- Claims
- Application Information
AI Technical Summary
Problems solved by technology
Method used
Image
Examples
specific Embodiment 1
[0028] (1) Clean the TPX membrane, and after vacuum drying, cover the surface with a layer of anodized aluminum template with a standard pore size. The pore size of the anodized aluminum template is 50 nm, the hole spacing is 100 nm, and the thickness is 50-70 μm. Put it into the substrate stage of the vacuum chamber of the plasma reactor, evacuate to 1Pa, then pass helium (He) until the pressure of the vacuum chamber reaches 10Pa, the irradiation time (etching time) is 200s, and the irradiation power is 150W. Stop the discharge, evacuate the vacuum chamber to 1Pa, and replace the gas in the vacuum chamber with nitrogen, repeat 2-3 times;
[0029] (2) Remove the aluminum oxide template on the surface of the TPX film, then fix it and put it into the substrate stage of the vacuum chamber of the plasma reactor, vacuumize to 1Pa, use oxygen (O 2 ) for surface activation, and the vacuum chamber pressure is 20Pa. The irradiation time is 20s, and the irradiation power is 150W. Stop...
specific Embodiment 2
[0031] (1) Clean the TPX membrane, and after vacuum drying, cover the surface with a layer of anodized aluminum template with standard pore size. The pore size of the anodized aluminum template is 200nm, the hole spacing is 500nm, and the thickness is 50-70μm. Put it into the substrate table of the vacuum chamber of the plasma reactor, evacuate to 1Pa, then pass helium (He) until the pressure of the vacuum chamber reaches 20Pa, the irradiation time (etching time) is 600s, and the irradiation power is 300W. Stop the discharge, evacuate the vacuum chamber to 1Pa, and replace the gas in the vacuum chamber with nitrogen, repeat 2-3 times;
[0032](2) Remove the aluminum oxide template on the surface of the TPX film, then fix it and put it into the substrate stage of the vacuum chamber of the plasma reactor, vacuumize to 1Pa, use oxygen (O 2 ) for surface activation, and the vacuum chamber pressure is 50Pa. The irradiation time is 120s, and the irradiation power is 200W. Stop the...
specific Embodiment 3
[0034] (1) Clean the TPX membrane, and after vacuum drying, cover the surface with a layer of anodized aluminum template with a standard pore size. The pore size of the anodized aluminum template is 50 nm, the hole spacing is 100 nm, and the thickness is 50-70 μm. Put it into the substrate stage of the vacuum chamber of the plasma reactor, evacuate to 1Pa, then pass argon (Ar) until the pressure of the vacuum chamber reaches 10Pa, the irradiation time (etching time) is 200s, and the irradiation power is 150W. Stop the discharge, evacuate the vacuum chamber to 1Pa, and replace the gas in the vacuum chamber with nitrogen, repeat 2-3 times;
[0035] (2) Remove the aluminum oxide template on the surface of the TPX film, then fix it and put it into the substrate stage of the vacuum chamber of the plasma reactor, vacuumize to 1Pa, use ammonia (NH 3 ) for surface activation, and the vacuum chamber pressure is 20Pa. The irradiation time is 20s, and the irradiation power is 150W. Sto...
PUM
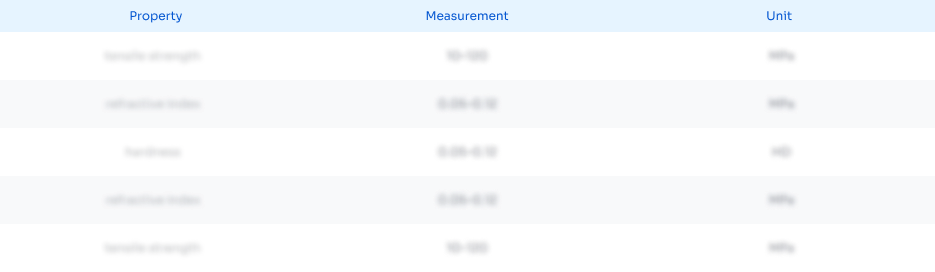
Abstract
Description
Claims
Application Information

- Generate Ideas
- Intellectual Property
- Life Sciences
- Materials
- Tech Scout
- Unparalleled Data Quality
- Higher Quality Content
- 60% Fewer Hallucinations
Browse by: Latest US Patents, China's latest patents, Technical Efficacy Thesaurus, Application Domain, Technology Topic, Popular Technical Reports.
© 2025 PatSnap. All rights reserved.Legal|Privacy policy|Modern Slavery Act Transparency Statement|Sitemap|About US| Contact US: help@patsnap.com