Method for synthesizing aliphatic/cycloaliphatic dicarbamate by one-pot reaction process
A dicarbamate and aliphatic technology, which is used in the synthesis of chemical product reaction intermediates, key intermediates aliphatic/cyclic dicarbamate, and non-phosgene synthesis of isocyanates, which can solve the problem of catalyst dosage. Large, low activity, no industrialization conditions, etc., to achieve the effect of less catalyst dosage, high atom utilization, and satisfying industrialization conditions
- Summary
- Abstract
- Description
- Claims
- Application Information
AI Technical Summary
Problems solved by technology
Method used
Image
Examples
Embodiment 1
[0051] Add 0.5mol 1,4-cyclohexanediamine, 0.8mol urea, 5mol methanol and 0.008mol sodium acetate into a 500ml self-circulating reaction kettle with electromagnetic stirring and automatic temperature control system, and pass N 2 Replace the air in the kettle. Under magnetic stirring conditions, the temperature was raised to 180°C at a rate of about 5°C / min. After 10 hours of reaction, the reactor was cooled to room temperature and samples were taken for HPLC analysis. The results showed that the conversion rate was 96% and the selectivity was 88%.
Embodiment 2
[0053] Add 0.5mol of hexamethylenediamine, 1.5mol of urea, 4.5mol of ethanol and 0.005mol of calcium acetate into a 500ml self-circulating reactor with electromagnetic stirring and automatic temperature control system, and pass N 2 Replace the air in the kettle. Under magnetic stirring conditions, the temperature was raised to 270°C at a rate of about 3°C / min. After 8 hours of reaction, the reactor was cooled to room temperature and samples were taken for HPLC analysis. The results showed that the conversion rate was 98% and the selectivity was 95%.
Embodiment 3
[0055] Add 0.5mol 4,4'-diaminodicyclohexylmethane, 1.0mol urea, 3.5mol n-propanol and 0.004mol zinc acetate into a self-circulating reactor with a volume of 500ml equipped with electromagnetic stirring and automatic temperature control system. N 2 Replace the air in the kettle. Under magnetic stirring conditions, the temperature was raised to 350°C at a rate of about 8°C / min. After 5 hours of reaction, the reactor was cooled to room temperature and samples were taken for HPLC analysis. The results showed that the conversion rate was 91% and the selectivity was 89%.
PUM
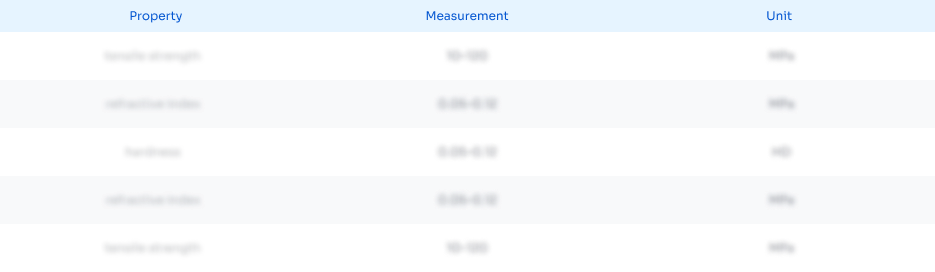
Abstract
Description
Claims
Application Information

- R&D
- Intellectual Property
- Life Sciences
- Materials
- Tech Scout
- Unparalleled Data Quality
- Higher Quality Content
- 60% Fewer Hallucinations
Browse by: Latest US Patents, China's latest patents, Technical Efficacy Thesaurus, Application Domain, Technology Topic, Popular Technical Reports.
© 2025 PatSnap. All rights reserved.Legal|Privacy policy|Modern Slavery Act Transparency Statement|Sitemap|About US| Contact US: help@patsnap.com