LTPS technology
A process and evaporation technology, applied in the field of LTPS process, can solve problems such as complex process, affecting product production yield, long production time, etc., and achieve the effect of reducing cost, shortening time and improving productivity
- Summary
- Abstract
- Description
- Claims
- Application Information
AI Technical Summary
Problems solved by technology
Method used
Image
Examples
Embodiment Construction
[0029] The following embodiments of the present invention are designed according to the principles of the present invention, and the present invention will be further described below in conjunction with the accompanying drawings and specific embodiments.
[0030] Such as Figures 1 to 5 As shown, the LTPS process of the present embodiment comprises steps as follows:
[0031] S1. On the glass substrate (heat treated at 600°C), the thickness of PECVD evaporation to prevent impurity penetration is buffer oxide layer;
[0032] S2. Using PECVD or LPCVD, the evaporation thickness is Single crystal silicon (a-Si) is used as the source and drain of the transistor (Transistor);
[0033] S3. In order to complete the LTPS non-laser (Non laser) method of silicon crystallization, ALD equipment is used to vapor-deposit Ni or sputter tens of atoms in atomic units. the Ni;
[0034] S4. Using a furnace (Furnace) to crystallize silicon under the condition of about 600° C. for one hour t...
PUM
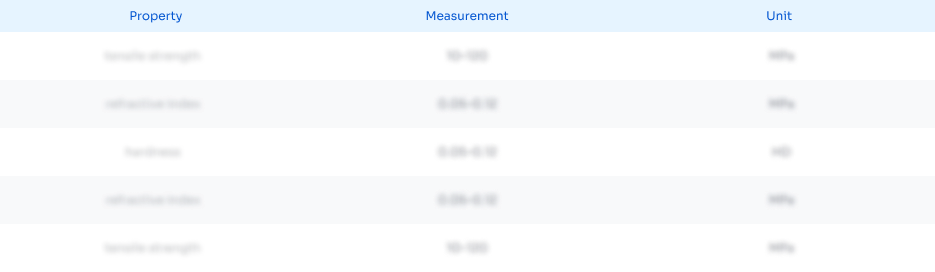
Abstract
Description
Claims
Application Information

- R&D
- Intellectual Property
- Life Sciences
- Materials
- Tech Scout
- Unparalleled Data Quality
- Higher Quality Content
- 60% Fewer Hallucinations
Browse by: Latest US Patents, China's latest patents, Technical Efficacy Thesaurus, Application Domain, Technology Topic, Popular Technical Reports.
© 2025 PatSnap. All rights reserved.Legal|Privacy policy|Modern Slavery Act Transparency Statement|Sitemap|About US| Contact US: help@patsnap.com