A melting and forging composite metal additive manufacturing device
A manufacturing device, metal additive technology, applied in the direction of the forging press drive device, etc., can solve the problems of difficult to achieve forging strength, limited application range, low strength of parts, etc., achieve large temperature gradient, promote grain refinement, eliminate loose effect
- Summary
- Abstract
- Description
- Claims
- Application Information
AI Technical Summary
Problems solved by technology
Method used
Image
Examples
Embodiment
[0026] A melting and forging composite metal additive manufacturing device, such as figure 1 As shown, it includes base 1, main support 2, molten metal ladle 3, three-axis servo motion system 4, nozzle 6, workbench 7, guide sleeve 8, forging head 9, turntable 10, high-speed motor 11, connecting rod 12, Crankshaft 13, servo motor 14, control unit 15.
[0027] The base 1, the main support 2, the workbench 7 and the turntable 10 constitute a base unit, the main support 2 is arranged on the base 1, and the workbench 7 is located in the main support 2 for placing the workpiece 5 to be processed.
[0028] The molten metal bag 3 and the nozzle 6 constitute the deposition unit, the molten metal bag 3 is fixed on the main support 2, the nozzle 6 is connected under the molten metal bag 3, and the molten metal in the molten metal bag 3 is deposited on the surface to be processed through the nozzle. The workpiece 5 surface.
[0029] The forging head 9, the guide sleeve 8, the connecting...
PUM
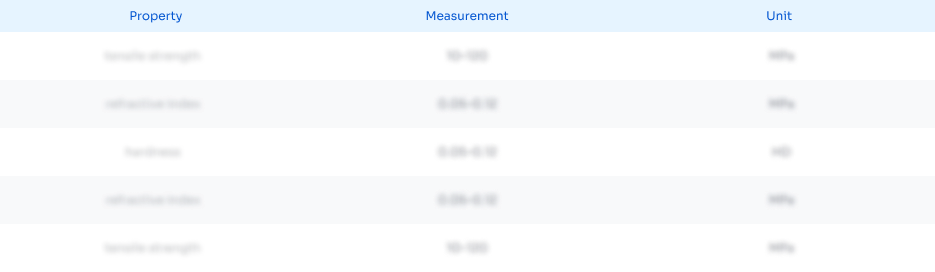
Abstract
Description
Claims
Application Information

- R&D Engineer
- R&D Manager
- IP Professional
- Industry Leading Data Capabilities
- Powerful AI technology
- Patent DNA Extraction
Browse by: Latest US Patents, China's latest patents, Technical Efficacy Thesaurus, Application Domain, Technology Topic, Popular Technical Reports.
© 2024 PatSnap. All rights reserved.Legal|Privacy policy|Modern Slavery Act Transparency Statement|Sitemap|About US| Contact US: help@patsnap.com